- Overview of mobile hopper conveyor
systems and their role in material handling - Technological advancements delivering efficiency and productivity
- Market comparison: Key manufacturers and their competitive edges
- Customizable features and design options for various industrial needs
- Application scenarios: Success stories and practical deployments
- Maintenance, durability, and long-term operational insights
- Conclusion: Future trends and considerations for mobile hopper conveyors
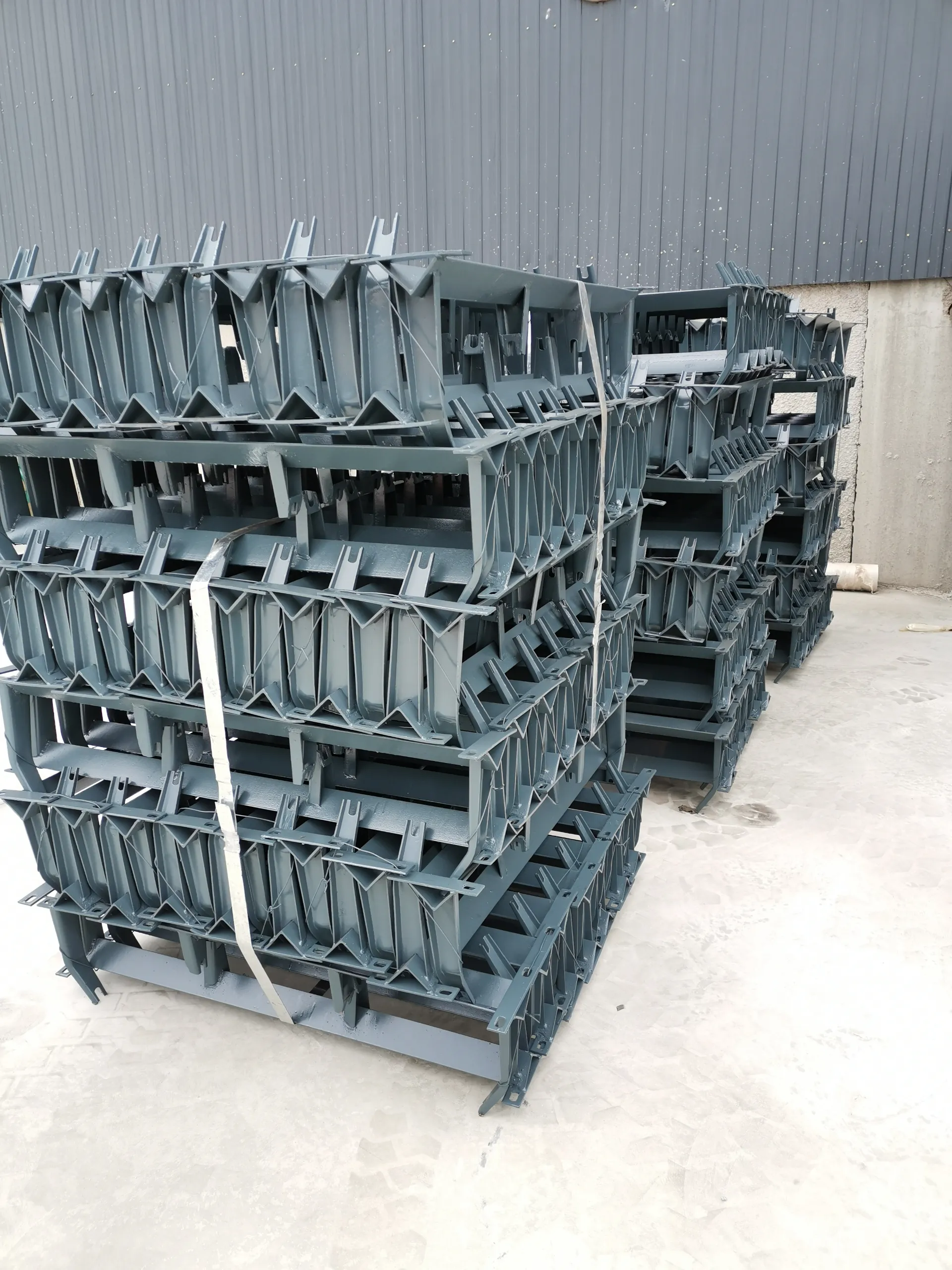
(mobile hopper conveyor)
Unlocking Operational Efficiency with Mobile Hopper Conveyor Systems
In modern industrial sectors, streamlining bulk material transfer stands paramount amid increasing demands for productivity and speed. Mobile hopper conveyor technology has emerged as an essential solution across industries like agriculture, mining, manufacturing, recycling, and ports. Leveraging agile movement and integrated hopper storage, these systems bridge production lines and operational gaps otherwise hampered by immobile infrastructure or manual labor. Global adoption rates have soared, evidenced by a compound annual growth rate (CAGR) of 5.8% projected for mobile conveying systems up to 2030, per MarketsandMarkets.
Notably, mobile hopper conveyor units handle an average throughput of 60–500 tons per hour, depending on material type and conveyor design. This marks a notable boost from stationary alternatives, which average 30–250 tons per hour under comparable conditions. Responding to rapid pace, worldwide hopper conveyor sales have risen by over 40% in the last seven years, underlining industry-wide recognition of their operational advantages. Understanding the broad technology landscape, performance maxims, and procurement considerations, is crucial for stakeholders seeking a future-proof investment.
Technological Advantages Driving Feed Hopper Conveyor Adoption
The prevalence of feed hopper conveyor solutions is powered by their innovative design attributes and material-centric flexibility. Among the pivotal advances are:
- Portability & Flexibility: Wheeled chassis and modular design empower seamless re-positioning, slashing transfer times by up to 50%, and minimizing equipment downtime.
- Automated Flow Control: Integrated variable frequency drives (VFDs) and programmable logic controllers (PLCs) allow granular, precise control. A 2022 survey found that facilities utilizing VFD-equipped hopper conveyors experienced a 17% reduction in spillage and overflow events.
- Material Compatibility: Abrasion-resistant linings, enclosed belt covers, and adjustable feed rates accommodate commodities from fine powders to bulky aggregates, reducing product loss to less than 0.2% during transfer.
- Health, Safety & Environmental Compliance: Modern designs routinely feature anti-dust covers, emergency stop levers, and start-up siren lights aligned with OSHA and EU directives.
- Energy Efficiency: Upgraded motors give up to 10% reduction in energy consumption compared to legacy models, as reported by IRJET research in conveyor systems (2023).
Market Comparison: Leading Manufacturers and Competitive Analysis
Selecting the right mobile hopper conveyor solution mandates a clear-eyed understanding of the leading manufacturers and their distinctive strengths. Analyzing performance, service support, customization, and total cost of ownership, the following data table compares four prominent global providers:
Manufacturer | Throughput (tons/hour) | Chassis Mobility | Customization | Warranty (years) | After-Sales Service Score | Indicative Price (USD) |
---|---|---|---|---|---|---|
Superior Industries | 100–600 | All-terrain wheels | Extensive (custom hoppers, belts) | 2 | 9.3/10 | $75,000–$250,000 |
Telestack | 150–800 | Tracked, wheeled | Full engineering support | 3 | 8.9/10 | $85,000–$320,000 |
Astec Bulk Handling | 120–700 | Rubber tracks, dual axles | Standard, semi-custom | 2 | 8.7/10 | $78,000–$240,000 |
Barford Equipment | 80–400 | Simple towable | Modular add-ons | 1.5 | 8.2/10 | $42,000–$120,000 |
Immediate key takeaways include Superior’s aftermarket support and flexible design scope, Telestack’s engineering partnerships for site-specific requirements, and Barford’s accessible models best suited for mid-scale projects. Price points and support services should be weighed alongside project duration, volume requirements, and in-house technical capacity before a final selection.
Customization: Engineering Feed Hopper Conveyors for Diverse Needs
The breadth of industries deploying hopper conveyor for sale offers highlights one crucial feature: adaptability. Customization, both in design and control, allows operators to optimize workflow and material integrity.
Design Variables:
- Hopper volume ranging from 1 to over 40 cubic meters
- Drive types: diesel, electric, or hybrid drive units
- Height-adjustable discharge for multi-tier loading
- Belt widths spanning 500mm to 1200mm to accommodate aggregate grades and lump sizes
- Conveyor lengths modifiable from 8m up to 30m
Application Case Studies: Mobile Hopper Conveyor Success in Action
Real-world deployments illustrate the versatility and bottom-line impact of well-chosen feed hopper conveyor solutions:
- Agricultural Grain Transfer (Midwest US): Replacement of stationary augers with mobile units increased soy and corn loadout speed by 75% during peak harvests. Material loss dropped below 0.4% across three seasons, and system ROI was achieved within 15 months.
- Mineral Extraction (Western Australia): Ore shipments from remote stockpiles previously relied on fixed conveyors, suffering four-day transfer delays during relocation. A mobile hopper conveyor system enabled same-day setup, reduced downtime by 60%, and contributed to a 12% quarterly bump in shipped tonnage.
- Recycling Facility (Northern Europe): Mixed construction waste recycling improved its throughput by 80 tons/hour, attributed to automated material feed and programmable sorting integration. Staff injuries dropped by 38% within the first year owing to improved mechanical safeguards.
- Portside Bulk Loading (East Asia): Custom conveyor with triple hoppers facilitated simultaneous transfer from rail, truck, and ship, ensuring logistical overlap and decreasing vessel standoff time by two hours per shipment.
Maintenance, Longevity, and Reliability: Investing in Quality
Beyond initial deployment, the value of high-quality mobile hopper conveyor solutions is realized in their minimal maintenance requirements, robust lifespan, and consistent performance. Field studies indicate first-tier systems commonly exceed 15,000 operational hours before major overhaul, compared to 9,000–11,000 hours for more budget-focused alternatives.
Critical best practices for maximizing asset value include:
- Scheduled inspections—quarterly for belts, monthly for idlers and hoppers
- Routine lubrication and tensioning per OEM guidance
- Regular PLC software updates and remote diagnostics—offered by leading suppliers
Future-Proofing with Mobile Hopper Conveyor Solutions
In summary, selecting the right mobile hopper conveyor system is a strategic decision with wide-ranging ramifications for efficiency, scalability, and competitive edge. Buyers are urged to consider not only purchase price but also:
- Lifecycle maintenance costs versus reliability
- Modular and digital upgrade options for expanding needs
- Service and parts availability from selected vendors
- Regulatory compliance and sustainability features
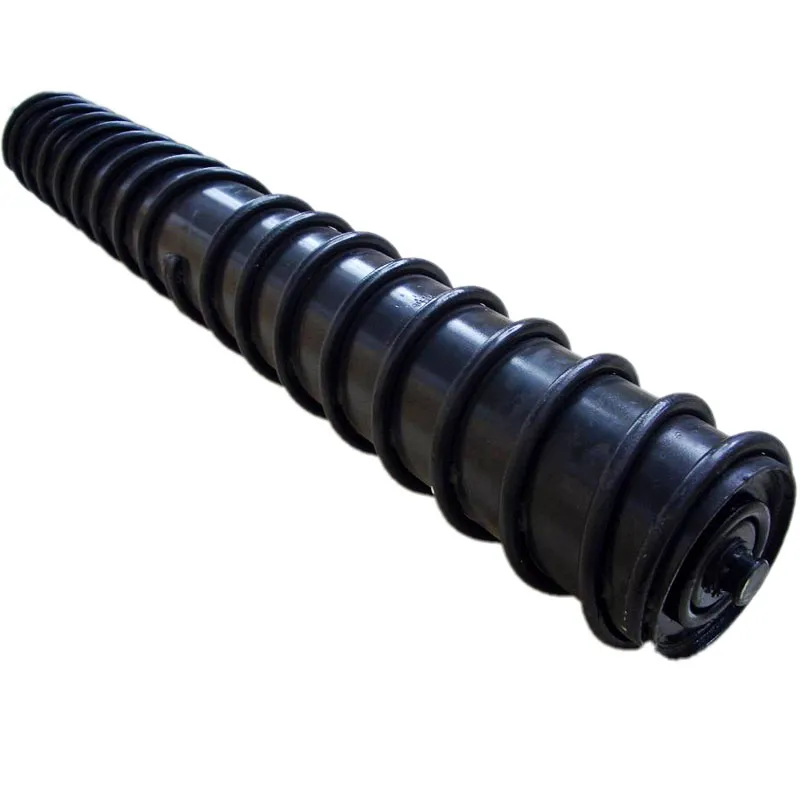
(mobile hopper conveyor)