- Introduction to Case Conveyor Solutions and Market Overview
- Key Technical Advantages of Modern Roll Case Conveyor Systems
- Comparative Analysis: Major Manufacturers in the Market
- Customization: Tailored Case Conveyor Solutions for Every Facility
- Case Conveyor Applications Across Diverse Industries
- Case Study: Implementing Case Conveyor in a Beverage Distribution Center
- Future Prospects and Final Perspectives on Case Conveyor Systems
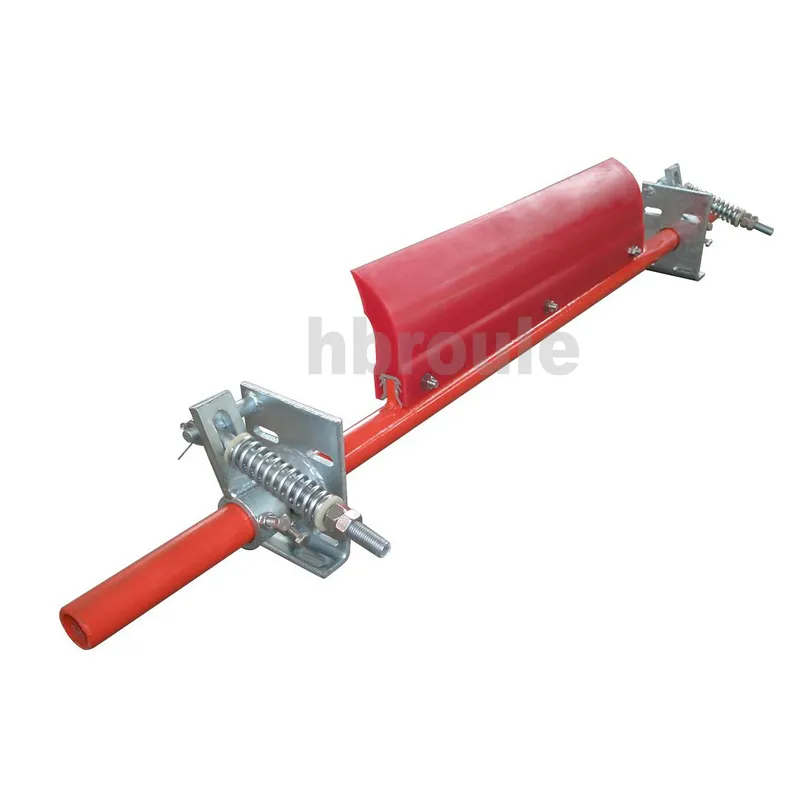
(case conveyor)
Exploring the Case Conveyor Market: Data, Demand, and Value Generation
In recent years, the case conveyor
market has exhibited significant growth as industries pursue higher throughput and efficiency standards. Market research projects the global conveyor systems market indicating a CAGR of 4.5% through 2028, with case conveyor adoption playing a pivotal role. As e-commerce expands, warehouses and production plants worldwide deploy case conveyors to automate handling, reduce manual labor, and meet rapid order fulfillment expectations. An estimated 35% of newly automated logistics centers utilize advanced case conveyor solutions, reflecting their critical role in enabling scalable operations. Facility operators report up to a 30% improvement in workflow speed and a reduction in workplace injuries related to manual case handling, underscoring the transformative impact such systems deliver. As digital transformation accelerates operational goals, case conveyor technologies stand at the forefront of driving competitive advantage and value within the supply chain sector.
Technical Superiority: Unlocking Features of Contemporary Roll Case Conveyor Solutions
Advances in roll case conveyor engineering have delivered substantial improvements in load management, throughput consistency, and system flexibility. State-of-the-art systems now incorporate intelligent sensors for automated case alignment and gap optimization, improving flow rates by up to 20%. Brushless motor technology reduces energy consumption by nearly 15% over legacy models, while modular frame designs allow for seamless integration with scanners, sorters, and robotic pickers.
High-precision rollers—manufactured to near-zero tolerance—minimize vibration, protecting fragile cargo and ensuring step-free transitions between conveyor segments. Noise reduction technologies deliver a safer, quieter workspace, with decibel levels decreasing by up to 35%. Such features empower facilities to boost efficiency and minimize product handling errors. Furthermore, modern systems routinely leverage IoT connectivity, providing real-time monitoring, maintenance alerts, and productivity analytics for predictive maintenance and continuous process optimization.
Manufacturer Comparison: Performance, Service, and Cost Analysis
Selecting the right case conveyor provider involves evaluating equipment functionality, customization capability, and long-term value. The following table details comparative data for three leading manufacturers in the roll case conveyor market:
Parameter | Manufacturer A | Manufacturer B | Manufacturer C |
---|---|---|---|
Max Throughput (cases/hr) | 7,000 | 5,500 | 6,800 |
Power Consumption (kWh) | 2.5 | 2.9 | 2.3 |
Standard Warranty (years) | 3 | 2 | 3 |
Customization Options | Extensive | Moderate | High |
IoT Enabled | Yes | No | Yes |
Typical Lead Time (weeks) | 10 | 7 | 12 |
Annual Maintenance Cost (% of unit price) | 5% | 6% | 4% |
Average Customer Rating (out of 5) | 4.7 | 4.3 | 4.6 |
Manufacturers A and C are notable for their high throughput and extensive customization, making them suitable for facilities with unique layout or process needs. Manufacturer B, while offering shorter lead times, provides less flexibility in system configuration. IoT integration is rapidly becoming a market differentiator, influencing total cost of ownership and long-term system reliability.
Customization: Crafting Precision-Fit Case Conveyor Solutions
Achieving optimal efficiency hinges on a conveyor solution that fits the exact requirements of the operation. Contemporary suppliers deliver modular, scalable case conveyor systems that adapt to any plant size, workflow, or product profile. Custom modifications may include variable speed control, incline or decline sections, accumulation zones, or built-in scales for automated weighing.
HVAC suppliers, for instance, rely on heavy-duty rollers tailored for oversized, fragile cargo, while food distribution centers might integrate stainless steel-coated belts and antimicrobial surfaces for hygiene compliance. Engineering teams typically leverage digital 3D modeling and factory acceptance testing to iterate design concepts and minimize installation disruption. This collaborative approach ensures seamless integration with legacy equipment and warehouse management systems (WMS). As a result, tailored roll case conveyor solutions are proven to cut integration timelines by up to 25% and boost ROI through bespoke performance optimization.
Real-World Applications: Versatility of the Case Conveyor
Case conveyors deliver essential logistics support and operational agility across a broad spectrum of industries. In pharmaceutical manufacturing, roll case conveyor lines are deployed for high-volume, tightly regulated shipping operations, ensuring compliance and batch traceability. For ecommerce fulfillment centers, automated case conveyors drive peak performance during high-velocity order cycles such as Cyber Monday, sustaining rate accuracy even when processing over 10,000 cases per hour.
Beverage producers utilize case conveyors to automate the movement of breakable bottles and heavy crates, using zero-pressure accumulation to prevent mixing and reduce damage. Automotive factories depend on robust designs capable of conveying large, irregular-shaped component cases while providing fast changeovers between product runs. Across nearly all sectors, case conveyor technologies facilitate automated sorting, palletizing, and cross-docking, demonstrating unmatched versatility in handling diverse packaging, carton strength, and stacking configurations.
Case in Action: Streamlining Beverage Distribution with Integrated Conveyor Solutions
A leading beverage distributor recently overhauled its central warehouse using an integrated roll case conveyor system. Prior to the upgrade, manual case movement limited throughput to 3,200 cases per hour, with significant labor costs and frequent product handling injuries. The facility partnered with a top-tier manufacturer to install a customized modular conveyor line featuring high-efficiency drive motors, vision-based barcode scanners, and dynamic case diverters.
Post-implementation, the distribution center recorded a 117% throughput surge—now processing over 7,000 cases per hour. Error rates in order assembly declined by 40% due to automated routing and real-time inventory validation, while annual labor costs fell by $480,000. The company also cited an 18% reduction in energy usage, aligning with their corporate sustainability targets. This transformation underscored the technology’s immense contribution to scalability, traceability, and workplace safety, offering a compelling template for similar high-volume distribution facilities.
Looking Forward: The Case Conveyor Advantage in an Automated Future
As demand for agile, scalable logistics intensifies, the adoption of advanced case conveyor technology will only accelerate. Innovations in machine learning and process automation promise to further optimize material flow and predictive maintenance, while seamless integration with robotics and digital control networks enhances facility responsiveness. Businesses seeking to outperform in fast-evolving markets will prioritize conveyors that combine technical excellence with tailored functionality. These systems are not simply transport mechanisms—they are the nerve center of next-generation warehousing and fulfillment. For enterprises intent on maximizing operational throughput and long-term value, case conveyor solutions offer an irreplaceable foundation for continuous improvement and supply chain resilience.
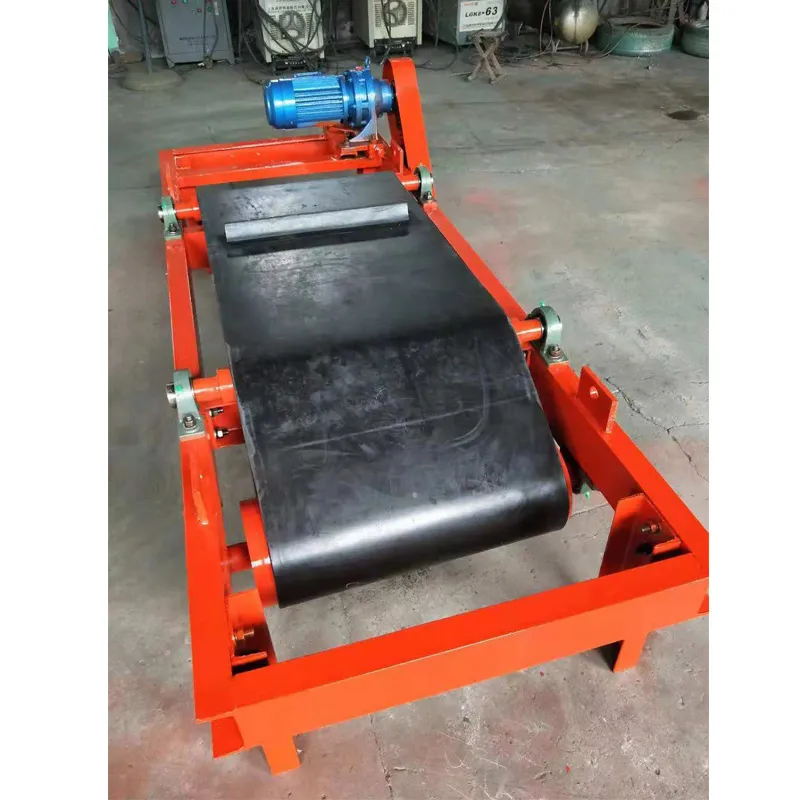
(case conveyor)