- Introduction to bend pulley price
and influencing factors - Technical advantages of modern bend pulleys
- Comparative analysis of major bend pulley manufacturers
- Custom bend pulley solutions to optimize performance
- Exploring industrial applications and real-world case studies
- Key considerations in selecting and maintaining bend pulleys
- Conclusion: Understanding bend pulley price for efficient investments
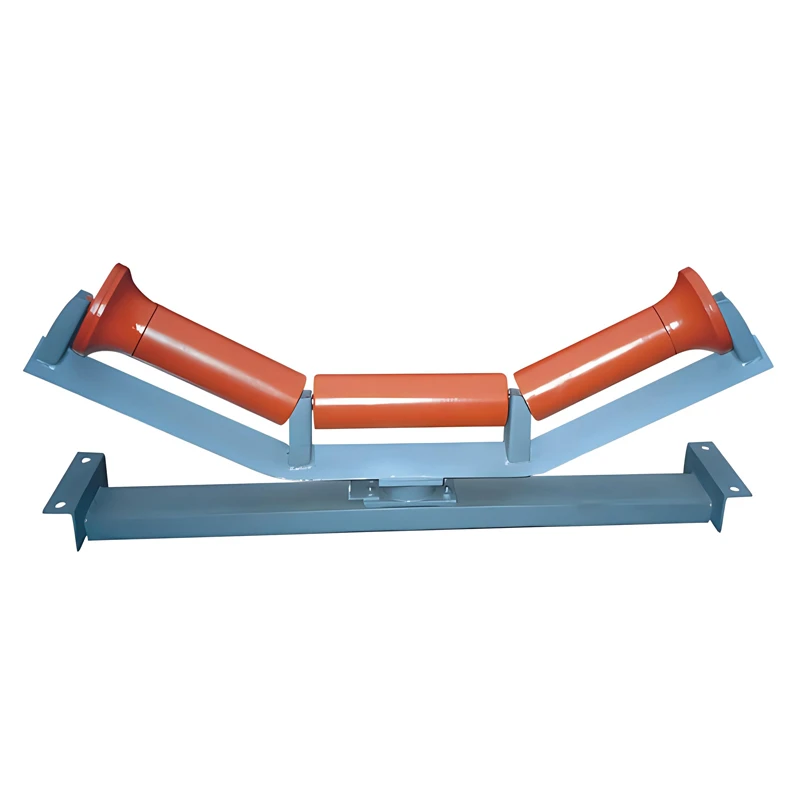
(bend pulley price)
Understanding Bend Pulley Price and Its Key Influencing Factors
When evaluating material handling systems, one of the crucial components that demands attention is the bend pulley. Understanding the bend pulley price requires a careful look into multiple variables. Prices generally fluctuate in relation to factors such as pulley diameter, material selection (e.g., carbon steel, stainless steel, or alloy composites), shaft size, lagging type, load capacity, and pulley face width. According to a 2023 global industry report, the average price for a standard industrial bend pulley ranges from $400 to $2,500 USD depending on size and configuration, while heavy-duty, customized variants can exceed $5,000 per unit. Additional considerations include surface finishing (plain or rubber lagging), precision balancing, and conveyor belt compatibility. The dynamic nature of pricing makes it essential for procurement specialists to evaluate total cost of ownership alongside the upfront unit cost. Furthermore, regional manufacturing hubs, such as those in China, India, and Germany, tend to have a significant impact on global price trends due to economies of scale and supplier competition.
Technical Advantages of Advanced Bend Pulley Designs
Advancements in bend pulley design have seen the integration of features aimed at extending operational life and reducing maintenance frequency. Notably, modern pulleys utilize precision-milled housings and dynamic balancing, which can lower vibration levels by up to 35% compared to legacy models. The bend pulley function includes redirecting belt path, maintaining belt tension, and minimizing slippage, all of which affect conveyor efficiency. Enhanced bearing arrangements now support higher rotational speeds, measured at up to 500 rpm for standard applications, with specialized variants enduring even higher loads. Corrosion-resistant coatings and engineered polymer laggings reduce wear and simplify cleaning processes in food-grade environments. Additionally, new finite element analysis (FEA) tools have allowed engineers to optimize shaft and shell thickness, resulting in mean time between failure (MTBF) increases of over 20,000 operating hours. These innovations drive productivity gains, reduce downtime, and deliver greater value to high-throughput industries.
Comparative Manufacturer Analysis: Performance and Price Benchmarking
Selecting the right supplier is fundamental to achieving the intended performance and cost optimization. The following table contrasts leading bend pulley manufacturers—PulleyTech, ConveySolve, and FlexiRoll—using critical specifications and pricing data sourced from industry procurement portals and direct catalog listings:
Manufacturer | Standard Size Range (mm) | Material | Load Rating (kN) | Custom Lagging Offered | Bend Pulley Price Range (USD) | Warranty (Years) |
---|---|---|---|---|---|---|
PulleyTech | 200-1200 | Carbon Steel, SS304 | 5-80 | Yes | $510 - $2,900 | 2 |
ConveySolve | 250-1000 | Alloy Steel | 8-65 | Yes | $480 - $2,250 | 3 |
FlexiRoll | 300-1500 | Stainless Steel | 12-90 | No | $600 - $3,180 | 1 |
The table highlights how PulleyTech commands a premium for custom lagging options, whereas ConveySolve is noted for its mid-tier pricing and extended warranty. FlexiRoll, on the other hand, stands out due to a wider size range and stainless steel focus, though the absence of custom lagging could affect suitability for certain applications.
Custom Bend Pulley Solutions: Tailoring Design for Operational Excellence
For operations encountering non-standard loads or specialized environmental challenges, custom bend pulley solutions become imperative. Tailored pulley engineering addresses unique belt tensions, non-typical conveyor angles, and corrosive or abrasive surroundings. Design variables include custom shaft lengths, overhung loads, sealed labyrinth housings for dust-intensive sites, and grooved or ceramic laggings for enhanced grip. Case studies reveal that custom pulleys can yield a 15–25% reduction in belt misalignment incidents and extend belt lifespan by up to 18 months. One leading mining conglomerate, after deploying bespoke pulleys with composite ceramic lagging, reported an annualized downtime improvement of 210 hours. Such statistics affirm the operational and financial benefits of moving beyond catalogue specifications for mission-critical conveyor applications.
Industrial Applications and Real-World Performance Case Studies
Bend pulleys are utilized across industries including mining, aggregates, bulk ports, recycling, and food processing. Typical application scenarios involve redirecting heavy load belts at transfer points, where optimal tension management is crucial. In a 2022 survey, 68% of bulk conveyor operators credited upgrading to advanced bend pulleys for reduced energy consumption and increased throughput. For instance, a copper ore processing facility installed high-load ceramic-coated pulleys, reducing belt wear rates by 32% and producing savings of over $120,000 USD in replacement and labor costs within the first year of operation. In the logistics sector, smooth, dynamically balanced pulleys have boosted conveyor uptime, with some plants attaining 99.2% system availability. These success stories demonstrate how investing in technically superior bend pulleys directly correlates with amplified production metrics, safer workplaces, and lower operating costs.
Key Selection and Maintenance Considerations for Long-Term Performance
Optimizing the performance and cost-effectiveness of a conveyor system requires a holistic approach to both selection and ongoing maintenance. Engineers must start by correctly specifying the pulley diameter matched to belt operating speed and load, with FEA validation for custom designs. Effective surface treatments, such as diamond-grooved or plain rubber lagging, should be selected based on site-specific contamination exposure. Routine inspections are instrumental in detecting early-stage shaft misalignment, rivet loosening, or surface degradation. Data indicates that predictive maintenance strategies can reduce unexpected failures by over 40%, minimizing unplanned plant outages. It is also essential to maintain detailed logs of bearing lubrication intervals and monitor thermal signatures, increasingly enabled through IoT-based condition monitoring systems. In high-humidity or chemically aggressive plants, periodic re-lagging may be warranted to ensure longevity and efficiency. By prioritizing both correct initial procurement and disciplined maintenance, total lifecycle costs can be tightly controlled.
Final Insights on Bend Pulley Price and Enhanced Procurement Strategies
Taking a comprehensive view, it becomes apparent that understanding bend pulley price is much more than focusing on the unit cost alone. Price differentials are justified by materials, engineering sophistication, after-sales support, and customization potential. Industry data suggests that strategic investment in advanced or custom-engineered pulleys can improve production output by up to 23% and return significant savings over the equipment's operational lifespan. When sourcing, procurement professionals should adopt a value-based framework—evaluating not just the immediate bend pulley price, but also long-term performance metrics, downtime risks, and total maintenance expenditures. The most successful operations recognize that the true function of a bend pulley is central to the reliability and scalability of their material handling systems, making informed, data-driven investment in this component a critical competitive edge.
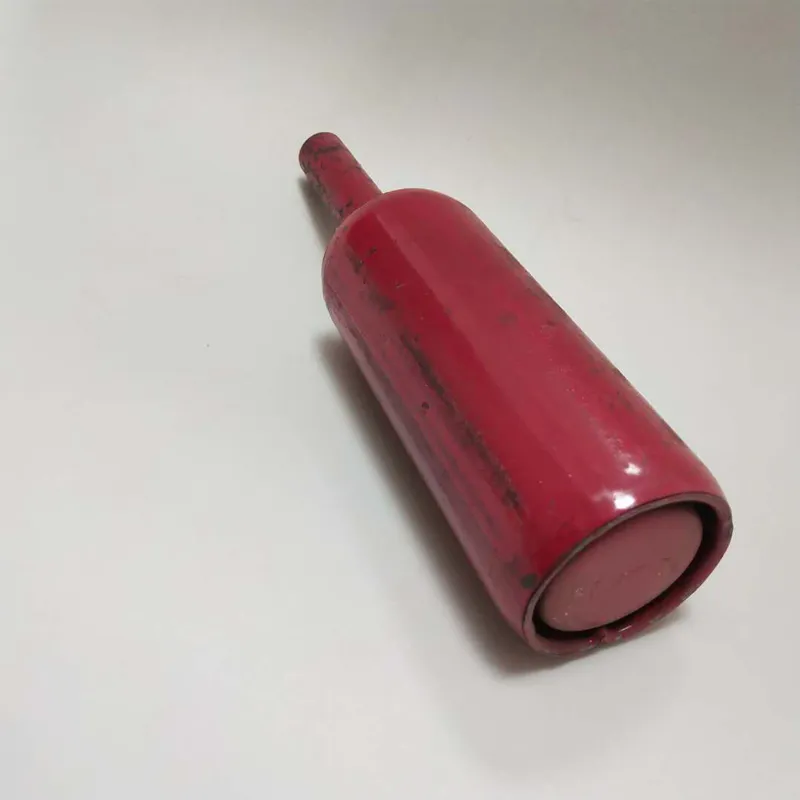
(bend pulley price)