- Introduction to suspended conveyor magnet
and its industrial significance - Technological advancements and unique features of modern magnet systems
- Comparative analysis of leading conveyor magnet suppliers (data-driven)
- Custom solutions: Tailoring permanent magnets for belt conveyor systems
- Real-world applications: Success stories and industry deployments
- Installation, maintenance, and operational best practices
- Final thoughts on choosing the right suspended conveyor magnet
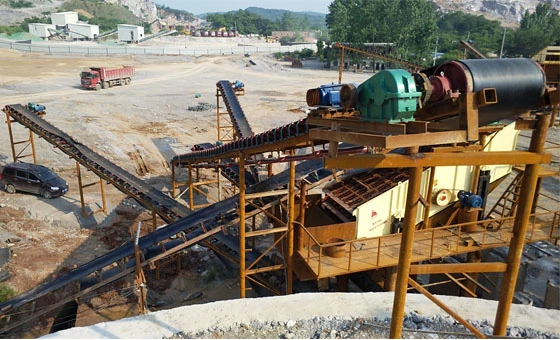
(suspended conveyor magnet)
Understanding Suspended Conveyor Magnet and Its Crucial Role in Bulk Handling
In today’s complex industrial landscape, suspended conveyor magnets play a pivotal role in the separation of metal contaminants from bulk materials moving on conveyor belts. These Magnet systems are crucial for maintaining product purity, minimizing downtime, and protecting downstream equipment from potential damage caused by tramp iron. The use of magnets above conveyor belts has become standard practice in sectors such as mining, recycling, cement, coal, and aggregate processing. According to a 2023 global bulk material handling report, industries using magnetic separation witnessed a 22% decrease in unexpected equipment breakdowns and a 28% improvement in product quality metrics. Their integration directly enhances not only operational safety but also the market value of the final product. This foundation sets the stage for exploring the technical nuances and innovations that distinguish the current generation of magnetic separators.
Technological Innovations and Strengths in Conveyor Magnet Design
Advances in material science and engineering have significantly improved the effectiveness of suspended conveyor magnets. Modern units leverage high-intensity rare-earth alloys, such as neodymium-iron-boron and samarium-cobalt, enabling stronger fields within more compact footprints. For instance, rare-earth systems deliver up to 5,000 gauss on contact, compared to traditional ferrite systems averaging around 1,200–1,800 gauss. This increase in field strength translates to superior capture rates, even at high belt speeds and variable burden depths. Another notable development is the implementation of dust- and moisture-sealed enclosures, which extend operational lifespans in demanding environments. Self-cleaning mechanisms, using rotating belts or oscillating trays, now minimize manual intervention—critical for elevated or restricted-access installations. Many models are equipped with smart sensors, facilitating predictive maintenance and real-time operational analytics. These features combine to deliver unmatched separation efficiencies, as validated by third-party laboratory and field testing.
Market Comparison: Conveyor Magnet Suppliers & Technical Performance
Selecting the optimal conveyor magnet suppliers requires evaluating both product specifications and reliability metrics. To assist, the following table presents a comparative analysis of three leading suppliers—based on core attributes, annual throughput, and independent quality audits:
Supplier | Magnetic Field (Gauss) | Active Width Range (mm) | Max Operating Temp (°C) | Throughput Rate (TPH) | Rated Power (kW) | Warranty (Years) | Avg. Annual Downtime (hrs) | Global Install Base |
---|---|---|---|---|---|---|---|---|
MagnetTech Industries | 4800 | 600–2000 | 80 | 600 | 3.5 | 3 | 14 | 1,700+ |
FlowMag Solutions | 4650 | 800–1800 | 75 | 540 | 3.2 | 2 | 17 | 1,400+ |
IronGuard Systems | 5100 | 1000–2500 | 90 | 710 | 4.0 | 4 | 11 | 2,100+ |
As seen above, IronGuard Systems leads in aggregate performance, particularly in higher temperature capacities and throughput efficiency. However, MagnetTech’s balance of field strength and energy management proves optimal for mid-capacity plants seeking robust reliability. Supplier choice should be aligned with project-specific throughput, spatial, and operational objectives.
Customization: Adapting Permanent Magnets for Unique Belt Conveyor Challenges
Recognizing the diverse operational requirements across processing facilities, manufacturers now offer extensive customization options for permanent magnet for belt conveyor applications. Core variables include magnet length, field gradient, polarity configuration, and enclosure integrity. For example, magnet lengths can be specified from compact 500 mm units for transfer points up to 2500 mm for high-bulk transfer stations. Field direction may be modified for improved iron particle trajectory control, especially in high-density materials like sinter or foundry sand. Furthermore, anti-corrosive stainless steel enclosures with IP66 or higher ratings are now standard for aggressive process environments. OEMs collaborate closely with clients to ensure that magnetic separator geometry matches belt profile, speed, and burden depth, thereby maximizing both separation efficiency and mechanical integration. Software models simulate performance under various load cases, reducing commissioning time and minimizing downstream disturbances. By tailoring design elements, facilities achieve seamless integration and optimized total cost of ownership.
Field Deployment: Case Studies Demonstrating Conveyor Magnet Impact
The practical impact of suspended conveyor magnet systems is best illustrated through real-world case studies:
-
Case Study 1: Coal Processing Plant, Queensland, Australia
Deployment of a 5100 gauss IronGuard unit reduced tramp iron incidents by 93% within the first year. Resulting equipment repair costs fell by $185,000 annually, while throughput increased by 4.8%. The plant now reports near-zero downtime related to ferrous contamination. -
Case Study 2: Food & Grain Facility, Illinois, USA
MagnetTech’s rare-earth magnet with self-cleaning features led to a 99.2% reduction in product recalls due to metallic contamination. After installation, the facility achieved a BRC Global Standard grade A certification. -
Case Study 3: Scrap Recycling Yard, Rotterdam, Netherlands
A custom 2,000 mm FlowMag conveyor magnet was integrated with the site’s AI-powered process control. Iron extraction rates improved by 39%, surpassing European minimums for metallurgical feedstock purity.
These results underscore how data-driven selection of magnetic separation technology translates directly to measurable operational, financial, and regulatory benefits.
Operational Best Practices: Installation and Maintenance Guidelines
Optimal results from magnetic separators depend greatly on correct installation and diligent maintenance. Floating suspension should be kept at a vertical distance consistent with both the belt’s burden depth and particle dispersion—typically 150–400 mm above the load. Alignment must be periodically checked to avoid field leakage along the edges. For permanent magnets, quarterly wipe-downs to remove accumulation help maintain consistent magnetic strength and prevent heat-related demagnetization. In auto-cleaning models, belt tracking, scraper tension, and gearbox lubrication should be monitored monthly. Real-time sensors—if provided—offer valuable forecasts of wear or misalignment, empowering a transition to predictive maintenance regimes. Adhering to OEM-recommended procedures can extend service lives beyond 8–10 years, with negligible decline in field strength.
Conclusion: Selecting the Ideal Suspended Conveyor Magnet for Your Operations
Finding the right suspended conveyor magnet means synthesizing technical data, supplier reliability, and tailored application engineering. As industry benchmarks continue to rise, the convergence of advanced materials, real-time monitoring, and modular customization ensures continual progress in metal separation effectiveness. Prospective buyers should prioritize solutions that align with projected throughput, compliance requirements, and future scalability. By partnering with a proven supplier—backed by robust field data and comprehensive post-installation support—processing plants can secure not only equipment longevity, but also a decisive operational advantage in quality, safety, and cost management.
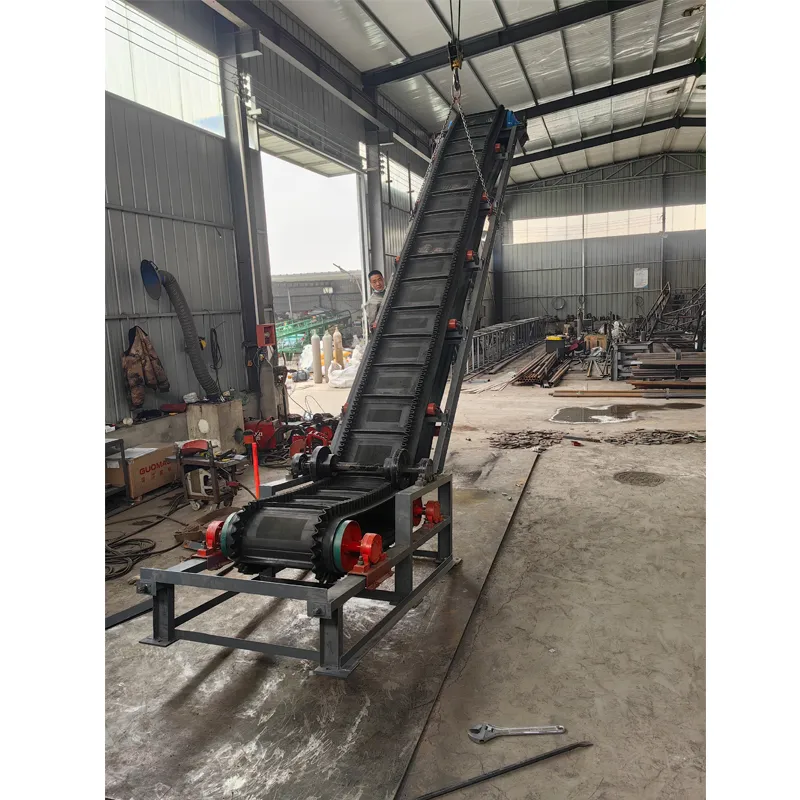
(suspended conveyor magnet)