- Introduction to accumulation roller conveyor
- Technical advantages and innovative features
- Comparison of leading accumulation conveyor system manufacturers
- Customization and modular design solutions
- Real-world application cases and industry impact
- Enhancements in efficiency, safety, and cost reductions
- Conclusion: Maximizing productivity with accumulation roller conveyor systems
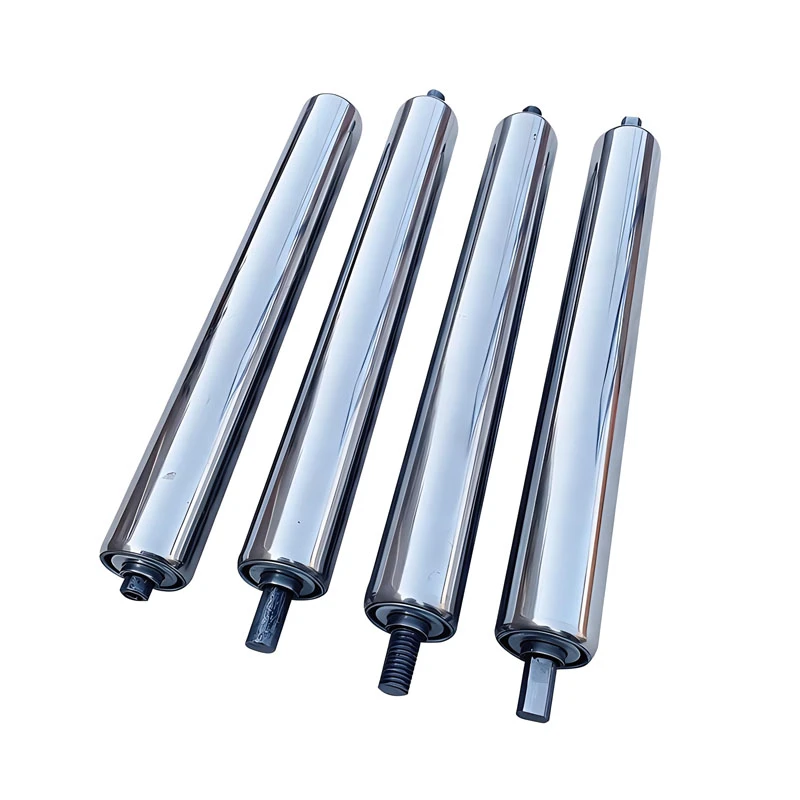
(accumulation roller conveyor)
Introduction to accumulation roller conveyor
The accumulation roller conveyor has revolutionized the handling and logistics industry, offering unparalleled control over the movement and spacing of goods on a production or distribution line. Characterized by its ability to allow packages to accumulate without line pressure, this technology avoids product damage, increases throughput, and improves workplace safety. In logistics, the efficiency and adaptability of accumulation conveyor systems define operational success, a fact reflected in recent market data. According to Statista, the global conveyor systems market value exceeded $7.46 billion in 2022, with accumulation conveyor representing a significant segment due to its widespread adoption in e-commerce, food processing, and automotive sectors. As supply chains become more demanding, the technical precision provided by accumulation rollers is fundamental to optimizing the movement and buffering of goods in dynamic, high-throughput environments.
Technical advantages and innovative features
Strategic deployment of accumulation roller conveyor systems brings marked improvements in operation. Unlike standard conveyors, accumulating conveyors deploy zero-pressure or low-pressure zones using sensors and regulated drive zones, preventing item-to-item contact and minimizing jams. Modern systems offer zone control using photo-eye sensors and feature integrated PLCs for dynamic speed adjustments. This ensures products disperse evenly or buffer when downstream processes demand. The latest technologies support high modularity, quick maintenance, plug-and-play replacement of rollers, and silent operation. Data from industry assessments shows that using accumulation conveyors can reduce product damage by up to 60&37; and increase overall system throughput by as much as 30&37;. These advantages translate directly to better resource utilization, particularly crucial for packaging, order fulfillment, and mixed-product handling lines where flexibility is key.
Comparison of leading accumulation conveyor system manufacturers
Choosing the right accumulation conveyor solutions involves evaluating leading suppliers on technology, customization, integration, and after-sales support. The table below compares four globally recognized manufacturers by key selection factors:
Manufacturer | Key Technology | Customization Options | Max Throughput (items/hour) | Noise Level (dB) | Warranty Period (years) |
---|---|---|---|---|---|
Interroll | Zero-Pressure ZPA Control, Modular Drives | High (Length, Width, Controls) | 5,000 | 56 | 5 |
Hytrol | EZLogic Accumulation, Integrated PLC | Medium (Custom Zone Sections) | 4,600 | 59 | 2 |
Dematic | Advanced Sensors, Dynamic Buffering | High (Customized for Industry) | 5,400 | 54 | 3 |
Honeywell Intelligrated | Smart Accumulation, IoT Integration | Medium (Optional Extensions) | 4,800 | 57 | 2 |
Analysis of this data reveals that technological leadership often correlates with longer warranty periods, lower noise emissions, and greater throughput. Interroll and Dematic excel at modular flexibility and industry-specific adaptations, whereas innovations from Honeywell focus on IoT and real-time tracking. This array of options allows businesses to align system selection closely with operational goals and integration needs.
Customization and modular design solutions
A defining trait of today’s accumulation conveyor systems is the degree of customization offered. Businesses can select between pallet, carton, or tote handling modes, add smart controls for mixed product or variable-weight operation, and configure system length, width, and incline per site constraints. Modular designs enable easy scaling—new conveyor zones or accumulation sections can be integrated with minimal disruption during expansions. Beyond standard steel frame builds, premium finishes and anti-static components are available for industries such as electronics and pharmaceuticals. Custom logic programming allows control of start/stop points, zone release timing, and priority merging. This ensures that a solution tailored for e-commerce order picking operates with different logic than a system designed for fragile glass bottle packaging. Data-driven customization helps minimize downtime for changeovers, ensuring that every project delivers not just fit, but future-proofing for evolving requirements.
Real-world application cases and industry impact
Numerous industries are capturing significant value from accumulation roller conveyor solutions. For example, an international electronics distributor implemented a 1.2-kilometer accumulation conveyor system to manage order surges during peak sales periods. The result was a 22&37; increase in picking rates and a 47&37; decrease in handling errors. Similarly, a food manufacturing plant reporting monthly product damages of over $180,000 prior to deployment, observed a 60&37; reduction in losses after switching to advanced zone-controlled accumulation conveyors. Automotive OEMs utilize accumulation conveyors to buffer painted car doors between painting and assembly, preventing surface defects and enabling continuous assembly line operation despite upstream or downstream delays. In pharmaceutical manufacturing, controlled accumulation protects sensitive blister packs and ensures precise sequence release, meeting stringent quality requirements. These success stories emphasize how accumulation conveyor systems serve as a backbone for efficiency and product protection in both high-volume and high-value environments.
Enhancements in efficiency, safety, and cost reductions
Deployment of sophisticated accumulation conveyor architectures delivers measurable advances across efficiency, safety, and financial performance. By eliminating line-pressure bottlenecks, teams benefit from reduced manual intervention and improved safety—workplace incident reports show up to a 35&37; decline in injuries related to material handling after introducing zero-pressure accumulation. Energy savings, often achieved by integrating run-on-demand motors and auto-idling controls, can drop conveyor-related power use by 20-40&37; annually. Maintenance needs are also minimized through modular components: replacing a zone drive or roller generally takes under 15 minutes, curtailing costly production downtime. When building a financial case, many businesses realize total project ROI within 12-24 months, attributed to reduced product damage, minimized labor costs, and increased throughput capability. For modern facilities facing competitive pressures to do more with less, accumulation conveyor systems represent a foundation upon which scalable, resilient, and cost-effective operations are built.
Conclusion: Maximizing productivity with accumulation roller conveyor systems
For organizations ready to embrace higher productivity and lower operational risk, investment in an accumulation roller conveyor or advanced accumulation conveyor systems is proven to yield immediate and compounding advantages. Manufacturers recognize that, with the right system selection and customization, accumulation conveyors transition from simple transport tools to strategic assets driving business growth. The integration of leading-edge sensor technology, modular construction, and robust control logic ensures each accumulation conveyor system delivers not only optimized throughput, but also increased reliability and safety. By leveraging data-driven system configuration and ongoing vendor support, companies across diverse industries capitalize on faster order fulfillment, better quality control, and future-ready scalability. Ultimately, accumulation conveyor solutions are at the heart of the next-generation automated supply chain, enabling businesses to deliver excellence, every day, at every stage.
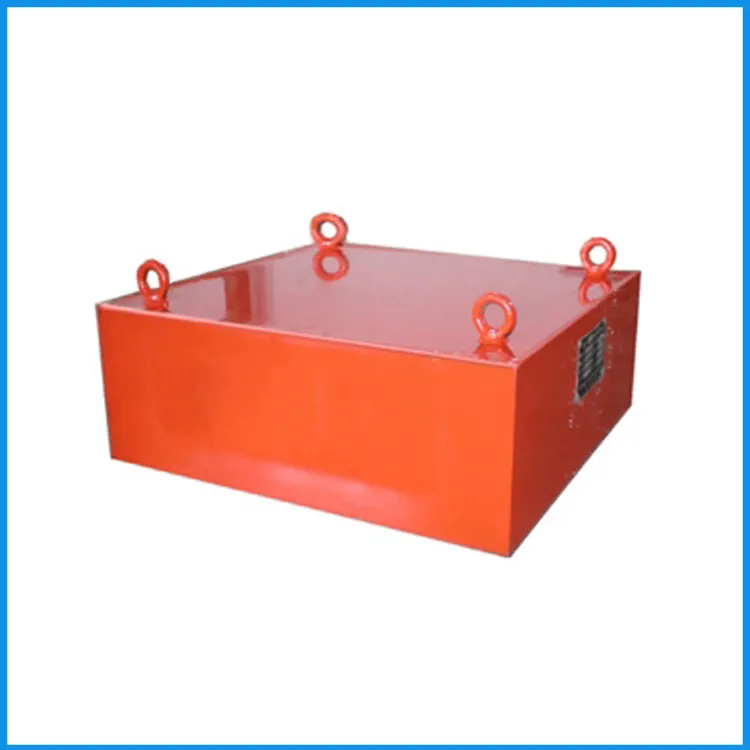
(accumulation roller conveyor)