- Introduction: Understanding Automated Warehouse Conveyor Systems
- Market Impact and Statistical Insights
- Technological Advantages of Modern Conveyor Automation
- Key Manufacturers: Comparative Analysis
- Custom Solutions and Integration Approaches
- Case Studies: Implementation in Real-world Warehouses
- Conclusion: Future of Automated Warehouse Conveyor Systems
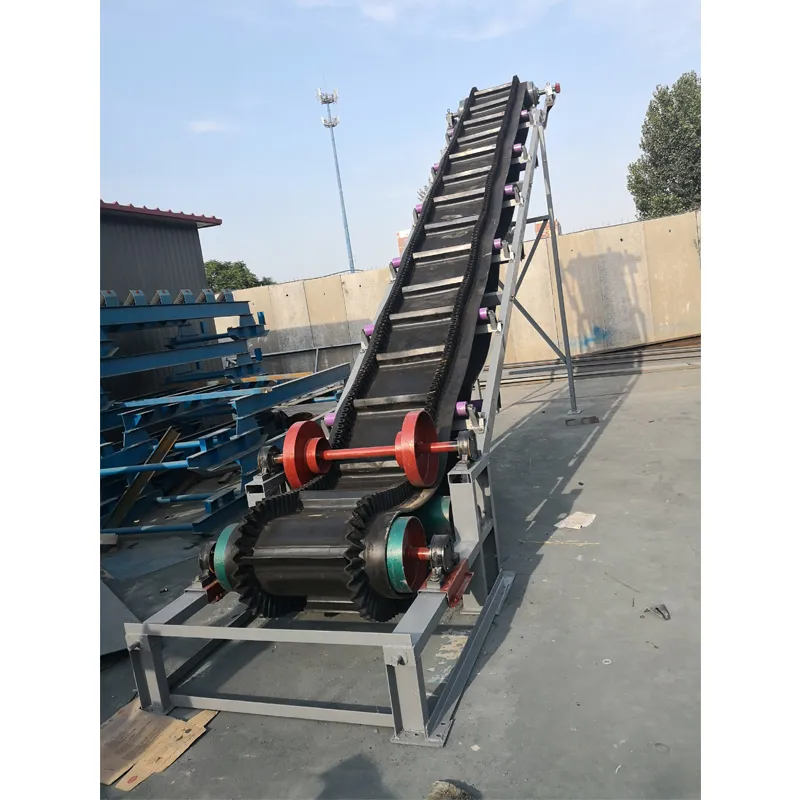
(automated warehouse conveyor systems)
Introduction: The Evolving Landscape of Automated Warehouse Conveyor Systems
As logistics and supply chain industries adapt to ever-increasing demands for speed and efficiency, automated warehouse conveyor systems
have emerged as a central solution. These advanced, computer-controlled systems streamline the movement of goods, improving productivity and accuracy within modern warehouses. Their integration spans across industries, revolutionizing traditional workflows and enabling warehouses to keep pace with e-commerce, retail, and manufacturing growth. Understanding their structure, core capabilities, and the pressing need for automation is pivotal for any organization seeking optimized intralogistics.
Market Impact and Statistical Insights
The influence of automated conveyor solutions on global logistics cannot be overstated. According to a 2023 report by MarketsandMarkets™, the worldwide automated material handling market—driven in large part by the adoption of conveyor automation—reached a value of USD 29.8 billion, projected to surpass USD 53.6 billion by 2028 at a CAGR of 12.3%. Warehouses leveraging these systems have reported throughput increases of 40%-75% and reductions in labor costs by up to 30%.
A survey by MHI noted that up to 80% of leading e-commerce providers consider automated conveyors a primary factor in meeting same-day delivery expectations. Industries ranging from pharmaceuticals to automotive supply chains have adopted this technology to address surging SKUs diversity, seasonality, and the need for touchless workflows—crucial during peak periods and disruptions alike.
Technological Advantages of Modern Conveyor Automation
Today’s automated conveyor systems bring transformative operational advantages. The latest systems utilize intelligent sensors, Machine Learning (ML) algorithms, and Internet of Things (IoT) connectivity. This results in lower energy consumption, adaptive routing, real-time diagnostics, and seamless integration with Warehouse Management Systems (WMS).
Notable features include:
- Dynamic Sorting: Real-time re-routing based on priority, destination, or size reduces bottlenecks.
- Energy Efficiency: Regenerative braking and variable-speed drives can cut energy costs by up to 25%.
- Predictive Maintenance: Remote monitoring means downtime can be reduced by 20-30% versus conventional conveyors.
- Modular Scalability: Systems can expand or shrink quickly in response to seasonal fluctuations or business growth.
Key Manufacturers: Comparative Analysis
Selecting the right partner is a pivotal step towards achieving optimal ROI and operational efficiency. The table below compares several global leaders in automated conveyor system manufacturing across criteria such as product range, technology, service support, and integration capabilities.
Manufacturer | Product Range | Key Technologies | Global Reach | Integration Support | Custom Engineering |
---|---|---|---|---|---|
Dematic | Modular & Flexible Conveyors, Automated Sorters | IoT, Predictive Analytics | 60+ countries | Seamless WMS, ERP | High |
Daifuku | High-speed Conveyors, AS/RS | Smart Sensors, AI Optimization | 50+ countries | Full SAP/WMS Stack | Very High |
Honeywell Intelligrated | Robotic, Modular, Pallet Conveyors | Machine Vision, RFID | Global | Integrated with 3rd-party apps | Moderate |
SSI Schaefer | Automated Conveyors, Shuttle Systems | IoT Control, Sustainability | 70+ countries | Advanced API integration | High |
Interroll | Roller Conveyors, Sorters | Plug & Play, Energy-Saving Motors | Europe, US, Asia | ERP/WMS ready | Medium |
When choosing among automated conveyor systems manufacturers, organizations should evaluate not just the technical prowess but also after-sales support, lead times, and the ability to deliver industry-specific customizations.
Custom Solutions and Integration Approaches
No two warehouses present identical operational challenges. Consequently, the best outcomes stem from tailored solutions developed in partnership with manufacturers and system integrators. Design processes typically begin with intensive data analysis—leveraging flow simulations, heat mapping, and SKU profiling.
Modern automated warehouse conveyor systems are highly adaptable, accommodating unique layouts, safety zones, and legacy system constraints. Integration with Warehouse Control Systems (WCS) or SaaS-based WMS ensures full visibility, while modular conveyor modules facilitate phased implementation strategies to minimize disruption.
For deep technical exploration, comprehensive guides and specifications, such as those available in automated conveyor systems PDF technical documents, are invaluable for operations managers and project engineers. These resources offer schematic diagrams, ROI calculators, and best-practice maintenance plans that expedite the specification and commissioning of bespoke systems.
Case Studies: Implementation in Real-world Warehouses
A growing body of case studies underscores the tangible benefits of conveyor automation. For instance, a leading European fashion retailer integrated a modular conveyor and sortation platform into its 60,000 sqm distribution center. Post-implementation, order throughput soared by 62%, errors plummeted by 78%, and overall picking time dropped from 6 hours to under 2 hours per shift.
Similarly, an automotive parts distributor in North America harnessed IoT-driven conveyors to manage 25,000 SKUs. The result was a 35% reduction in labor hours and inventory accuracy rates exceeding 99.5%. Seasonal scalability, enabled by modular design, allowed the warehouse to handle 2x the usual order volumes during peak seasons without additional square footage or staffing.
These cases, alongside hundreds more in retail, pharma, and e-grocery, demonstrate that the investment in robust conveyor automation yields both immediate productivity gains and lasting competitive advantages.
Conclusion: Harnessing the Power of Automated Warehouse Conveyor Systems
The future trajectory of automated warehouse conveyor systems is poised for continued innovation—leveraging AI, robotics, and cloud-based analytics to further redefine warehouse performance benchmarks. Organizations adopting next-generation conveyor technologies achieve not just higher throughput and cost efficiencies, but also agility and resilience in increasingly complex supply chains. As consumer expectations and SKU complexity grow, strategic automation becomes a non-negotiable driver of sustainable growth and service excellence.
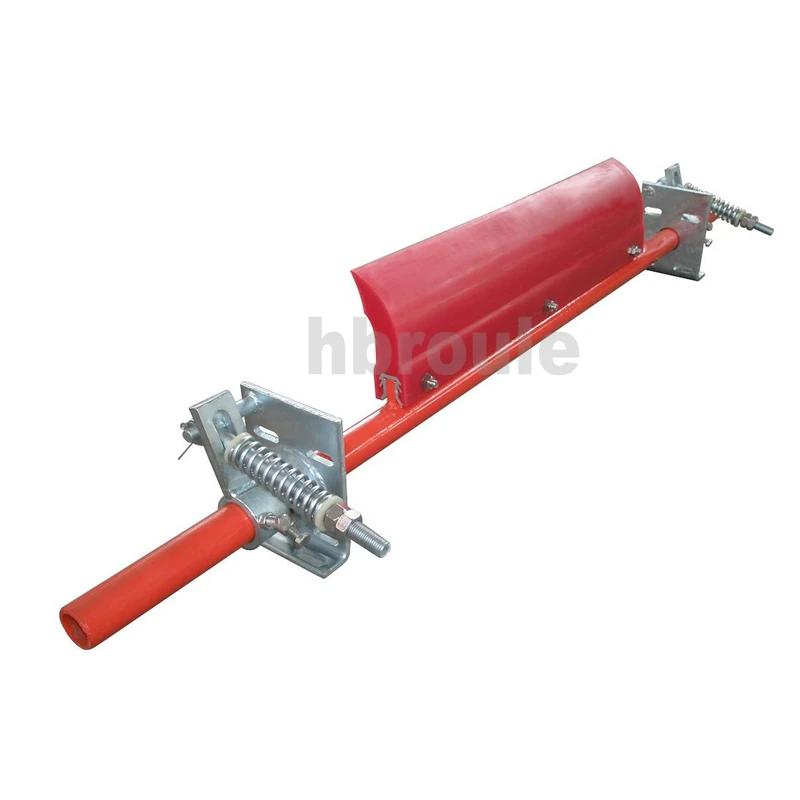
(automated warehouse conveyor systems)