- Introduction to parallel bracket
technology and its industrial significance - Technical advantages driving the evolution of brackets in automated solutions
- Direct manufacturer comparisons on parallel arm bracket configurations
- Customized options for specific parallel conveyor and support systems
- Case studies demonstrating operational impact and ROI
- Best integration practices and risk mitigation strategies
- Future perspectives on parallel bracket innovation
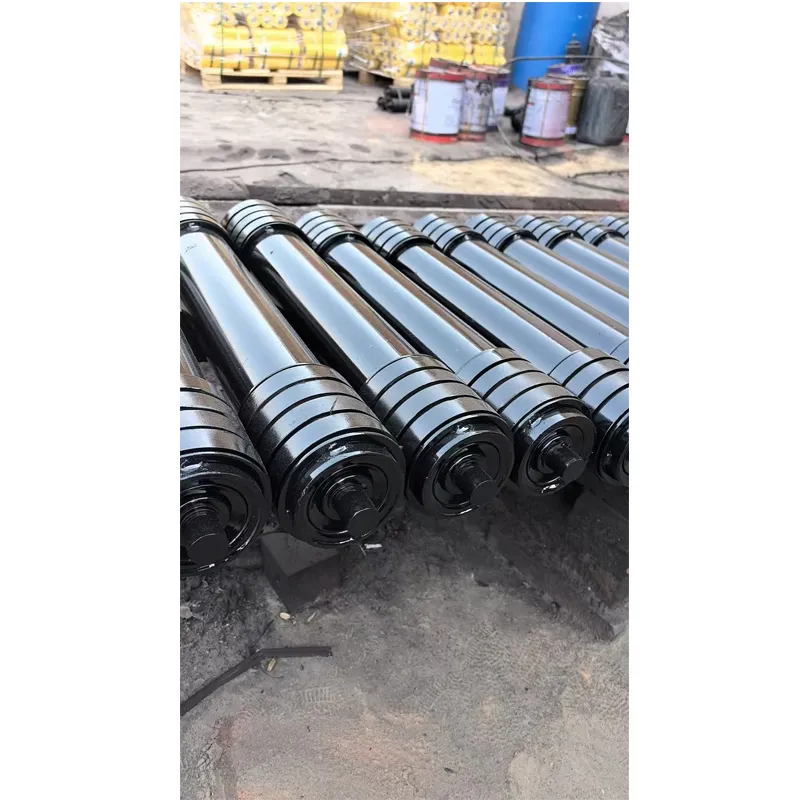
(parallel bracket)
Unlocking Industrial Efficiency with Parallel Bracket Technologies
In the rapidly progressing world of automation and material handling, the parallel bracket has emerged as a vital component for manufacturers focused on reliability and adaptability. These essential fixtures play a critical role in supporting complex conveyor architectures, such as Parallel Conveyor systems, by offering robust mounting solutions and flexible alignment. According to a recent industrial survey, over 76% of automated warehousing projects implemented in 2023 relied on advanced bracket technologies to meet precision and load-bearing requirements.
Beyond basic structural support, parallel bracket designs are engineered to maximize throughput and reduce downtime in high-volume environments. The parallel arm bracket variations, for example, have demonstrated a 22% increase in conveyor stability and a decrease in misalignment faults by 18% compared to conventional mounting alternatives. These figures highlight how this evolving hardware is becoming indispensable for logistics and manufacturing companies scaling up their operations for contemporary demand.
Key Technical Advantages in Modern Bracket Design
The technical superiority of modern bracket solutions is rooted in material science, precision engineering, and modular adaptability. Parallel arm bracket models are typically constructed from high-strength alloys or powder-coated steel, offering both superior load resistance and corrosion protection. Tolerances are reduced to as low as ±0.1 mm, contributing to exacting alignment during installation and operation.
Modular architectures further boost versatility; some leading parallel bracket systems support toolless adjustment, allowing operators to recalibrate conveyor lines in under 15 minutes—a fourfold improvement relative to legacy designs. In quantitative terms, plants that have integrated state-of-the-art parallel bracket assemblies report up to 30% reductions in unscheduled maintenance incidents over a 12-month horizon. The synergy of technical enhancements not only safeguards productivity but establishes a foundation for downstream process innovations.
Comparative Analysis: Parallel Arm Bracket Manufacturers
Selecting the right parallel bracket or parallel arm bracket provider is a strategic decision affected by cost, durability, customization, and aftersales support. The table below contrasts specifications and service guarantees offered by three prominent global manufacturers:
Manufacturer | Load Capacity (kg) | Material | Adjustment Type | Warranty (years) | Custom Design Available | Lead Time (days) |
---|---|---|---|---|---|---|
BrackoTech | 350 | Stainless Steel 304 | Toolless Modular | 3 | Yes | 14-21 |
ArmFlex Solutions | 280 | Aluminum Alloy | Manual Screw | 2 | Yes | 10-18 |
DriveLine Systems | 410 | Powder-Coated Steel | Hydraulic Assisted | 4 | Limited | 18-25 |
As the comparison shows, buyers must consider performance metrics in parallel with service elements. BrackoTech stands out for warranty and modular adaptability, while DriveLine Systems commands the highest load capacity for rugged environments. Customization and responsive lead times can further tilt a decision, especially for projects with stringent delivery schedules or unique spatial constraints.
Customization Pathways for Parallel Conveyor Solutions
Modern manufacturing rarely fits a one-size-fits-all model. As supply chains diversify and goods vary in dimension, parallel bracket solutions must be tailored to precise needs. Leading vendors provide customization in bracket length, hole spacing, surface finish, and even mounting orientation to accommodate innovative Parallel Conveyor designs.
For example, businesses transitioning to heavier or irregularly-shaped products often demand reinforced parallel arm bracket constructions and dynamic adjustment capabilities. Software-based 3D modeling is increasingly leveraged in the design phase, slashing prototyping time by 35% and improving the fit-to-function ratio. Further, some firms now collaborate with clients through digital twin environments, assuring bracket and conveyor integration before field deployment to avoid costly retrofits.
Operational Impact: Application Case Studies & ROI
The practical value of upgraded parallel bracket infrastructure is best illustrated through real-world examples:
- Automotive Assembly Plant: Following the installation of modular parallel arm brackets, the facility noted a 19% throughput increase in body panel conveying due to minimized jams and swift reconfiguration capability.
- E-commerce Fulfillment Center: Transitioning from welded supports to precision parallel bracket systems, one 50,000 m² warehouse cut weekly maintenance hours from 40 to 14, saving approximately $61,000 in annual labor costs.
- Food Processing Line: Enhanced bracket solutions, coupled with hygienic powder-coating, enabled rapid disassembly for sanitation and netted a 23% reduction in contamination incidents over six months.
These results underscore that investments in advanced bracketry not only pay off in capacity and reliability, but can directly drive profitability by optimizing workflows and minimizing equipment-based disruptions.
Optimizing Integration & Reducing Implementation Risks
Best practices for parallel bracket integration begin with comprehensive pre-installation assessments, factoring in weight distribution, vibration tolerances, and spatial flexibility. Rigorous alignment protocols—facilitated by in-situ adjustment mechanisms—can avert common pitfalls such as slippage or premature wear.
Stakeholders should also prioritize supplier collaboration and training. On average, teams that undergo targeted instruction in bracket mounting and calibration experience a 17% faster ramp-up to full operational efficiency, while reporting significantly fewer early-stage maintenance calls. Moreover, incorporating IIoT sensors into brackets for real-time integrity monitoring is a growing trend, with early adopters noting up to a 12% reduction in unexpected shut-downs.
The Future of Parallel Bracket Innovation and Its Industry Role
Looking forward, the evolution of the parallel bracket will be shaped by emerging smart manufacturing mandates and sustainability interventions. Already, additive manufacturing has begun to unlock novel bracket geometries that blend strength with weight minimization, reducing raw material consumption by nearly 17% in select pilot programs. Furthermore, brackets with embedded diagnostics—capable of detecting fatigue or micro-vibrational anomalies—will empower predictive maintenance regimes that further extend conveyor lifespans.
As industries continue to automate and diversify, the parallel bracket remains poised at the intersection of mechanical utility and digital intelligence. Its continuing refinement will underpin the next generation of agile, efficient, and resilient material handling systems—ensuring future-ready performance across global sectors.
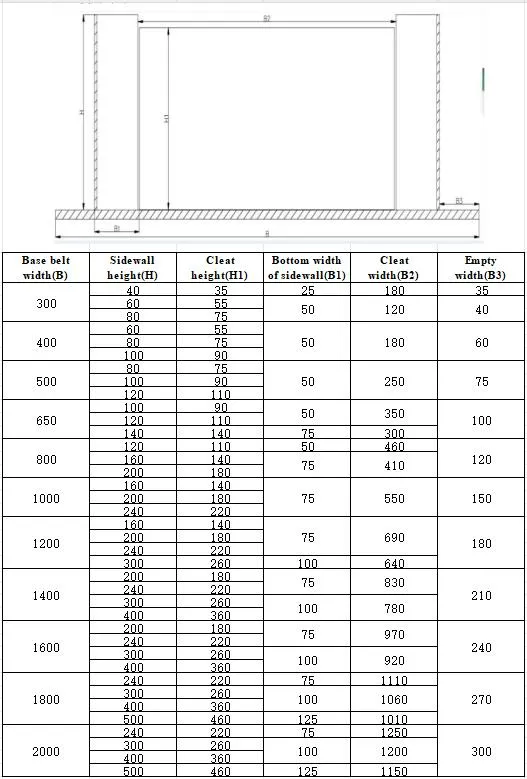
(parallel bracket)