- Introduction to accumulation conveyor systems
and their industrial relevance - Market Overview: Data-driven insights and technological evolution
- Technical Advantages: Mechanisms, efficiency, and productivity impact
- Manufacturer Comparison: Features, specifications, and pricing—visualized through a comparative table
- Customization: Tailoring accumulation conveyor solutions to unique operational needs
- Case Studies: Real-world applications and success metrics
- Conclusion: Future outlook for accumulation conveyor systems and user recommendations
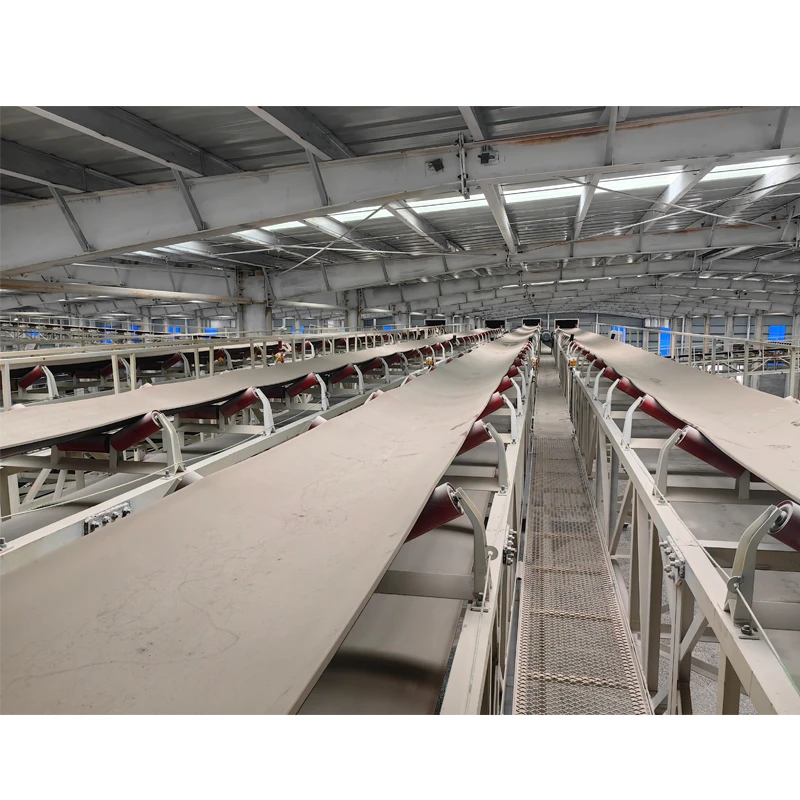
(accumulation conveyor systems)
Introduction: The Role of Accumulation Conveyor Systems in Modern Industry
Accumulation conveyor systems have become integral in optimizing intralogistics for diverse industries, including manufacturing, packaging, food processing, and distribution centers. As businesses strive for operational excellence and minimal downtime, accumulation roller conveyor solutions emerge as crucial assets to ensure the smooth and controlled movement of goods through various stages of production or distribution. Their modular architecture, seamless integration with existing conveyor infrastructure, and adaptability to various product types make them highly sought after in the current industrial landscape. The deployment of accumulation conveyor technology leads to reduced manual intervention, enhanced throughput, and precise product handling—elements central to lean manufacturing and automated warehousing. Early adoption sectors have seen marked improvements in facility output by as much as 20-30%, driven by fewer product jams and optimized space utilization.
Market Dynamics: Data Insights & Technological Evolution
The global market for accumulation conveyor systems is projected to reach $2.3 billion by 2028, growing at a compound annual growth rate (CAGR) of 6.7%. This upward trajectory is propelled by the exponential increase in e-commerce, a surge in automated material handling needs, and a persistent focus among enterprises towards Industry 4.0 integration. The ongoing transition from conventional conveyors to advanced accumulation conveyor installations has brought a notable expansion in technical capabilities, including zone-control for energy efficiency and sophisticated PLC programming for dynamic sequencing. In response, manufacturers are able to offer reliable and responsive accumulation solutions that both manage surges in product flow and facilitate zero-pressure accumulation, protecting product integrity. Statistical surveys reveal reductions of up to 40% in product damage incidents where accumulation conveyor systems replace traditional buffer zones—a testament to their efficacy.
Technical Excellence: Innovative Features and Productivity Impact
Accumulation roller conveyor solutions are distinctive due to their non-contact product handling, allowing for precise accumulation without physical pressure between products. Their modular construction facilitates scalability, enabling businesses to expand or reconfigure lines with minimal disruption. Technological enhancements such as photo-eye sensors, intelligent motorized rollers, and integrated data logging substantially improve line control and traceability. According to recent process audits, facilities utilizing sensor-driven accumulation conveyor systems reported a 35% decrease in downtime attributed to fewer bottlenecks and automated fault isolation. Furthermore, energy consumption analyses highlight reductions up to 25% when integrating accumulation conveyors with zone-driven motor controls, contributing to sustainability goals. Maintenance intervals are also extended, with proactive diagnostics minimizing unscheduled stoppages and prolonging equipment lifespan.
Manufacturer Comparison: Features, Specifications, and Pricing
Choosing the right accumulation conveyor requires evaluating a spectrum of factors including carrying capacity, energy efficiency, control systems, and overall cost. The table below provides a comparative overview of leading manufacturers based on recent market data, addressing critical differentiators for procurement and operational planning:
Manufacturer | Model | Max Throughput (Cartons/hr) | Zone Control | Energy Consumption (kWh/day) | Maintenance Interval (Months) | Price Range (USD) |
---|---|---|---|---|---|---|
Interroll | ACCM-700 | 3,500 | Yes | 28 | 18 | $13,000 - $19,000 |
Hytrol | EZLogic Gen3 | 3,200 | Yes | 31 | 20 | $15,000 - $22,000 |
Dematic | Accum-Lite 500 | 2,900 | Partial | 34 | 16 | $12,000 - $18,000 |
FlexLink | X85 Accum | 2,700 | Yes | 27 | 19 | $14,500 - $20,000 |
MHS | AccuSort-Plus | 3,450 | Yes | 29 | 21 | $17,000 - $25,000 |
This comparative snapshot illustrates the diversity in specifications available to buyers. Notably, models with robust zone control consistently demonstrate improved energy management and longer maintenance cycles, justifying potential premium investments for high-throughput environments.
Tailored Solutions: Customizing Accumulation Conveyor Installations
Adapting accumulation conveyor solutions to specific operational requirements is crucial for maximum return on investment. Leading integrators offer comprehensive customization options that address facility layout constraints, product types, and throughput objectives. Custom accumulations may include integration of stainless steel roller beds for hygiene-sensitive sectors, specialized low-noise motors for noise-critical environments, or dynamic zones for mixed product dimensions. End users can specify advanced safety interlocks, automated queue release controls, and system-level data interfaces for seamless communication with enterprise resource planning (ERP) platforms. Pre-engineered modules enable rapid deployment, while full bespoke engineering supports optimized layouts for legacy retrofitting or greenfield installations. Through site assessments and simulation modeling, vendors help customers balance the trade-off between conveyor footprint, accumulation capacity, and future scaling paths.
Application Case Studies: Transformative Results Across Sectors
Successful deployment of accumulation conveyor systems spans a broad spectrum of industries, delivering quantifiable improvements in efficiency and throughput. In the consumer electronics sector, a top-five manufacturer integrated an accumulation roller conveyor system into its assembly line, reducing manual handling and realized a 22% increase in daily output. In a food packaging facility, a transition from conventional conveyors to accumulation solutions led to a 40% reduction in product damage rates and a 30% cut in overall labor requirements. Automotive component suppliers reported that zero-pressure accumulation conveyors cut line bottlenecks and drove on-time order fulfillment rates to above 98.5%. Additionally, e-commerce fulfillment centers leveraging automated zone-control accumulation conveyor arrays decreased package sorting cycle times by 18%. These validated outcomes underscore the versatility of accumulation conveyor technology, from high-speed sorters in distribution hubs to precision handling of fragile goods in pharma supply chains.
Conclusion: Future Perspective on Accumulation Conveyor Systems
The trajectory for accumulation conveyor systems points toward even greater integration with smart factory ecosystems and artificial intelligence-driven predictive maintenance. The advancements in connectivity and modularity will continue to expand their applicability across new sectors. Investment in accumulation roller conveyor technology delivers consistent returns through enhanced throughput, minimized product damage, and improved energy efficiency. Decision-makers should partner with vendors that demonstrate adaptability, robust after-sales support, and forward-thinking innovation in accumulation conveyor design. Through evidence-based selection and ongoing process development, organizations can harness the full potential of accumulation conveyor solutions to drive operational excellence now and well into the future.
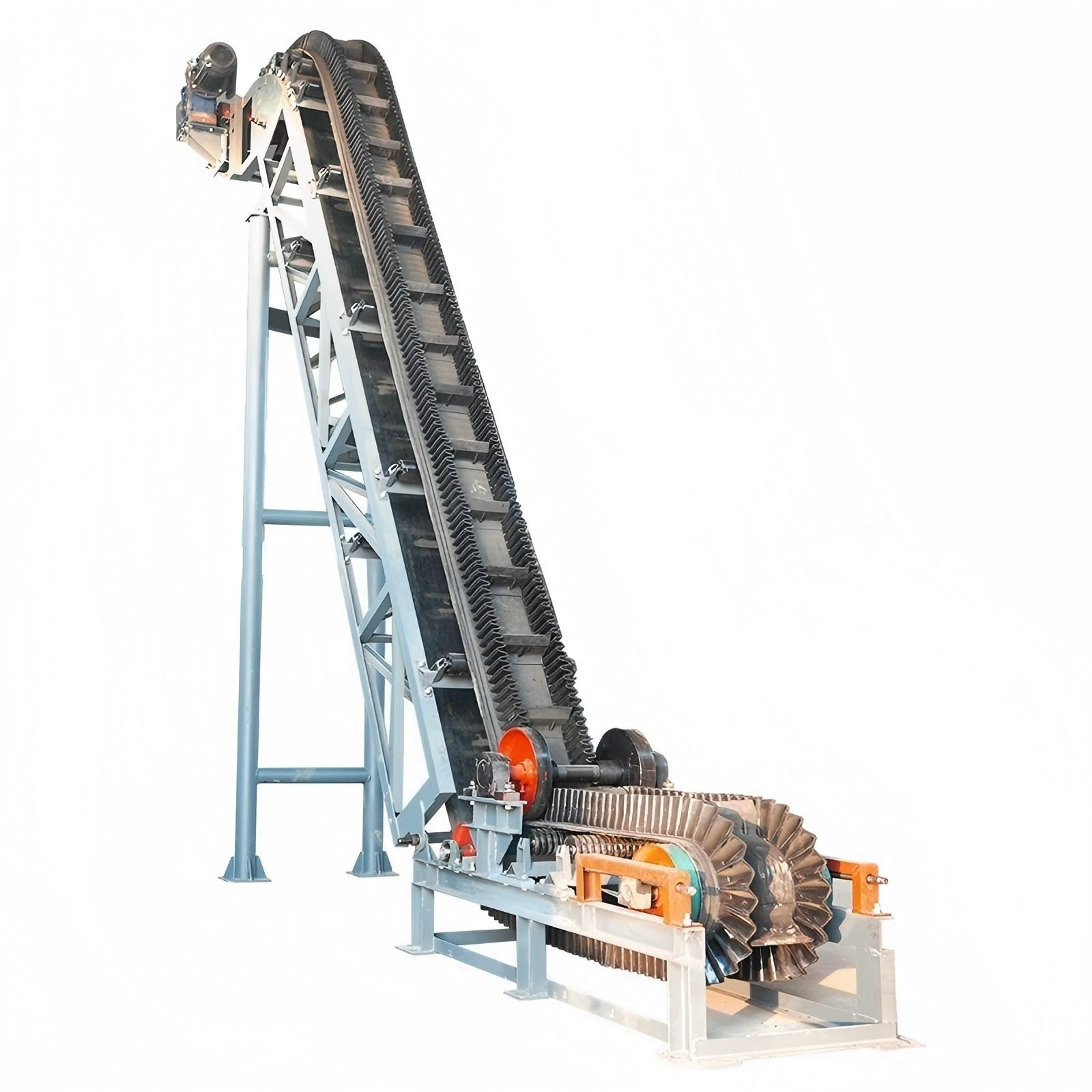
(accumulation conveyor systems)