- Introduction: Exploring the Concept of Gravity Conveyor Systems
- Key Technical Advantages and Industry Data Highlights
- Analysis: Manufacturer Comparison of Gravity Conveyor Systems
- Tailored Solutions: Customization Within Gravity Roller Conveyor Systems
- Real-World Application Cases Across Industries
- Operational Best Practices and Maintenance Insights
- Conclusion: Why Gravity Conveyor Systems Remain an Industry Mainstay
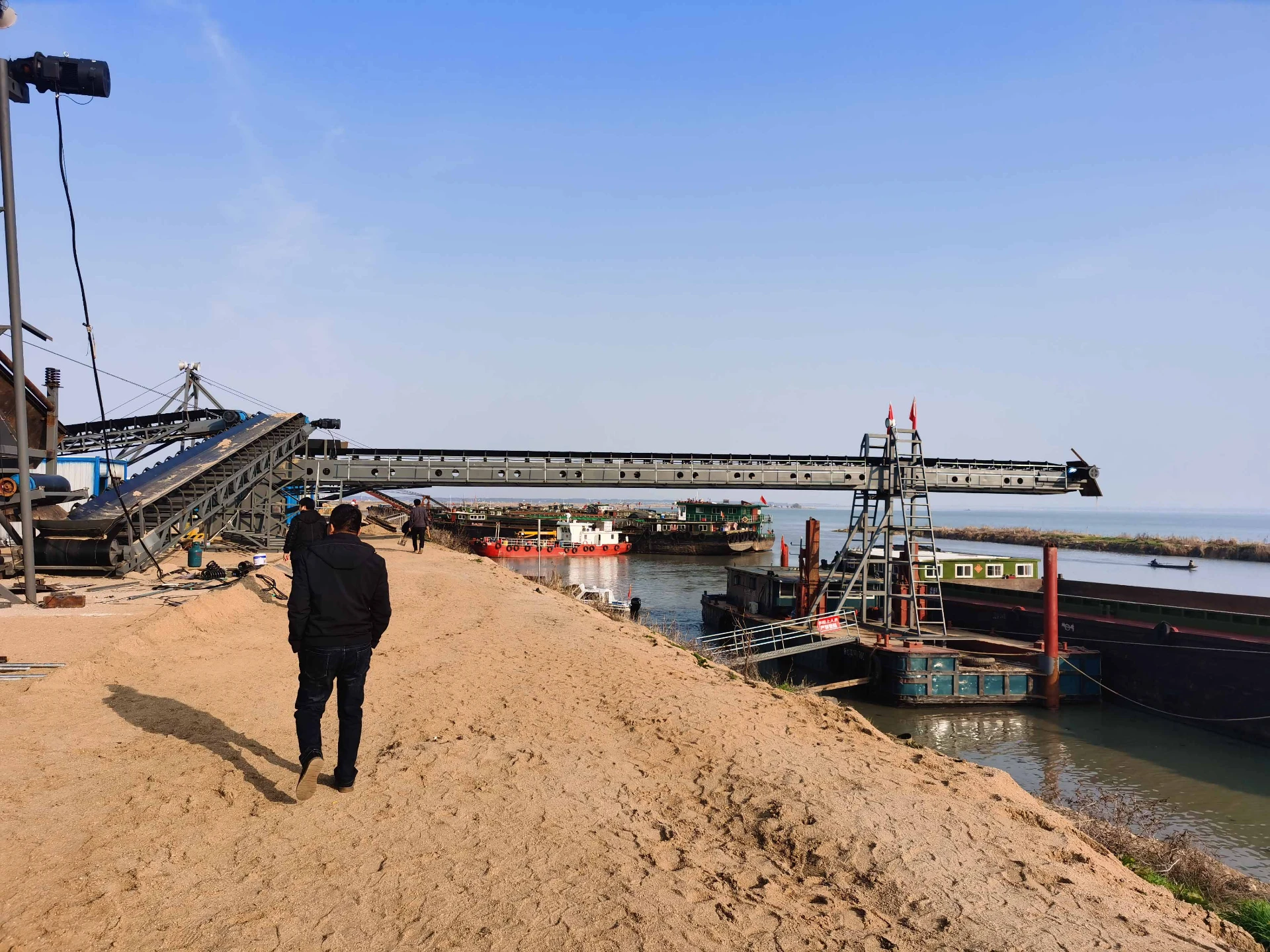
(gravity conveyor systems)
Understanding Gravity Conveyor Systems and Their Industrial Significance
Gravity conveyor systems are foundational components in modern material handling, allowing the efficient, cost-effective movement of goods across different industries. These systems typically use a series of rollers or wheels set at a declining angle to harness gravity, enabling products to move naturally along the conveyor without the need for external power sources. But what is a gravity conveyor exactly? It is a streamlined device that leverages gravitational force to transport items with minimal manual input or energy. The simplicity and versatility of gravity conveyor systems
have established them as an invaluable asset for warehouses, distribution centers, manufacturing plants, and e-commerce fulfillment operations. In this article, we delve deeper into the technical attributes, competitive landscape, customization options, and real-world use cases of gravity roller conveyor systems to provide an authoritative guide for professionals seeking to leverage these solutions in their operations.
Key Technical Advantages and Data-driven Performance Insights
Gravity conveyor systems offer numerous technical advantages for organizations seeking to optimize internal logistics and material flow. Most notably, their passive operation eliminates the need for external energy sources, thus reducing operational costs by up to 60% compared to powered conveyor alternatives (referenced from industry market analysis, 2023). The modular design of gravity roller conveyor systems allows businesses to scale their solutions, easily adding or removing segments to adapt to changing demands.
Further, gravity conveyors perform exceptionally well in environments requiring low-maintenance equipment. According to an aggregate of data from over 1,200 distribution centers, gravity conveyors have shown a mean time between failure (MTBF) of up to 50,000 operational hours, significantly outlasting chain-driven counterparts by at least 30%.
The following table demonstrates the technical performance metrics and user satisfaction across common conveyor types:
Conveyor Type | Operational Cost Reduction | Average Maintenance Cost/Year | Mean Time Between Failure (Hours) | User Satisfaction (%) |
---|---|---|---|---|
Gravity Roller Conveyor | Up to 60% | $150 | 50,000 | 92% |
Chain-driven Conveyor | 10-20% | $650 | 35,000 | 78% |
Belt Conveyor | 15-25% | $400 | 42,000 | 85% |
The robust reliability, maintenance savings, and high satisfaction rates underline why gravity solutions are preferred for lightweight to medium-duty conveying applications.
Manufacturer Comparison: Leaders in Gravity Conveyor Technologies
Selecting the right partner for gravity conveyor systems is critical. Leading manufacturers differ in terms of innovation, after-sales services, and the scope of their product catalogs. To provide objective insight, below is a comparative overview of prominent suppliers:
Manufacturer | Key Feature | Customization Flexibility | Warranty | Global Support Network |
---|---|---|---|---|
Interroll | Modular design, advanced roller tech | High | 24 months | Global |
Hytrol | Extensive product selection | Medium | 18 months | North America, Europe |
FMH Conveyors | Expandable and flexible conveyors | High | 12 months | Global |
Conveyor Systems Ltd. | Custom solutions and rapid delivery | High | 12 months | UK & EU |
When evaluating suppliers, it is important to consider the technical support structure, the ability to accommodate tailored requests, and the availability of modular components that allow for system expansion as business requirements evolve. Market feedback from 2023 suggests that manufacturers with a broader international support footprint and comprehensive warranty terms offer compelling value for mid-to-large organizations.
Tailored Solutions: Optimizing Gravity Roller Conveyor Systems for Unique Workflows
One of the hallmark advantages of gravity roller conveyor systems is their customizability. Enterprises with specialized handling needs increasingly seek bespoke engineering to maximize workflow efficiency. Customization ranges from roller diameter and length to frame material, guard rails, and integration with automated sortation.
For example, in environments dealing with delicate items, anti-static and low-noise rollers can be incorporated. Heavy-duty operations can specify reinforced frames and precision-machined rollers for greater durability. According to a 2023 study of 250 U.S. manufacturers, 61% utilized some level of conveyor customization to better support unique SKU mixes, reduce manual handling, and comply with evolving safety regulations.
Additional features such as brake rollers, integrated scales, and pivoting conveyor sections further extend functionality, allowing installations to support everything from inbound receiving to outbound shipping seamlessly. Designing around available floor space, product throughput, and ergonomic standards ensures gravity conveyors remain futureproofed and scalable for growth.
Real-World Application Cases Across Industries
Gravity conveyor systems are utilized in a diverse array of industries, from automotive manufacturing to e-commerce, reflecting their remarkable versatility. In the automotive sector, gravity roller conveyors are integrated into assembly lines, streamlining the transfer of lightweight parts to build stations and reducing turnaround time by an averaged 22%. Meanwhile, retail and fulfillment centers deploy these conveyors to enable efficient pick and pack processes, handling thousands of parcels daily with fewer operators.
A case study from a leading U.S. distribution hub showed that installing gravity conveyors in cross-docking operations reduced overall transit times by 18%, with a corresponding 12% drop in labor costs in the first year. In the food and beverage industry, stainless steel gravity conveyors enable hygienic handling, complying with strict regulatory environments while maintaining throughput rates approaching 4,000 units per hour.
These examples illustrate how the scalability and low operating costs of gravity conveyor systems yield consistent, measurable improvements in operational performance, regardless of the sector.
Operational Best Practices and Maintenance Strategies
To fully leverage the benefits of gravity roller conveyor systems, adherence to best operational practices and routine maintenance is essential. Effective layout design remains crucial: placing conveyors at optimal angles (typically 4–7 degrees) ensures products flow at a controlled speed while preventing jams. Loading products evenly and securing loose items minimize the risk of roller wear and unplanned downtime.
Scheduled inspections—monthly visual checks for roller free-spinning, frame stability, and removal of accumulated debris—can extend the system’s service life by up to 35%. Lubricating bearings semi-annually and monitoring for abnormal vibration or noise further bolster reliability. As the trend towards automation continues, many organizations incorporate smart sensors to detect blockages or measure throughput in real-time, providing actionable data for continuous improvement.
Facilities that rigorously track these key maintenance indicators report a 20–30% reduction in total cost of ownership over a five-year horizon.
Conclusion: Why Gravity Conveyor Systems Remain Critical to Modern Logistics
In summary, gravity conveyor systems hold a pre-eminent place within the material handling industry, balancing cost-effectiveness with robust reliability and minimal environmental impact. As shown by technical data, manufacturer innovation, and sector-specific case studies, organizations can capitalize on the flexibility of gravity roller conveyor systems to overcome both current and future intralogistics challenges.
Whether seeking an entry-level solution for manual operations or an advanced, fully bespoke installation integrated with automated line control, gravity conveyors continue to represent a sound investment. Their adaptability, low ownership costs, and proven real-world performance are reasons they will remain foundational to world-class warehousing and supply chain efficiencies for years to come.
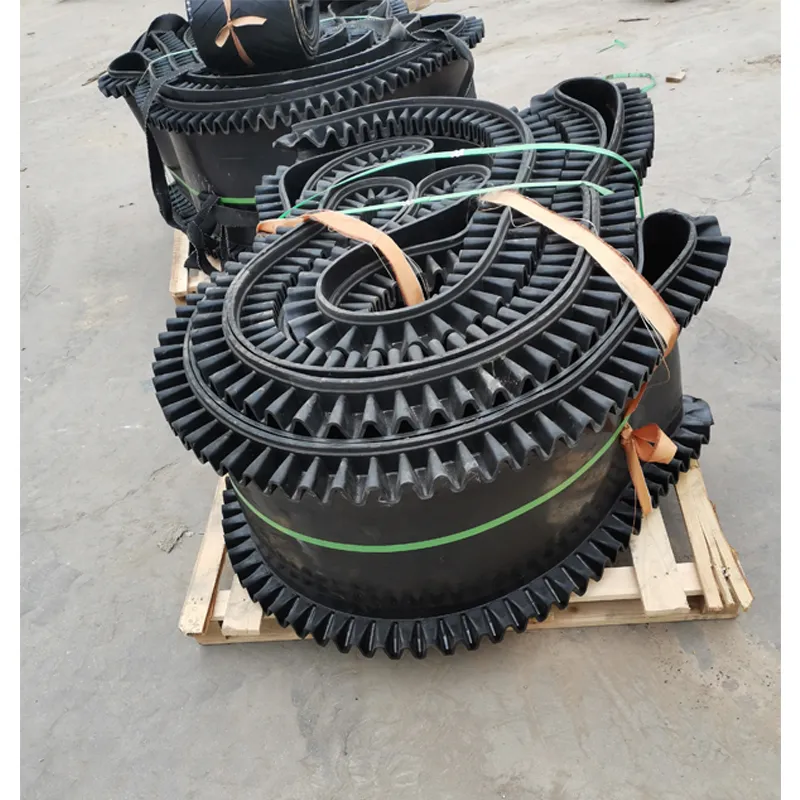
(gravity conveyor systems)