- Industrial impact of modern bulk handling solutions
- Engineering advancements in belt conveyor systems
- Material-specific technical configurations explained
- Leading manufacturer comparison analysis
- Customization for industrial processing scenarios
- Real-world case studies across multiple industries
- Selecting optimal belt conveyor systems for sale
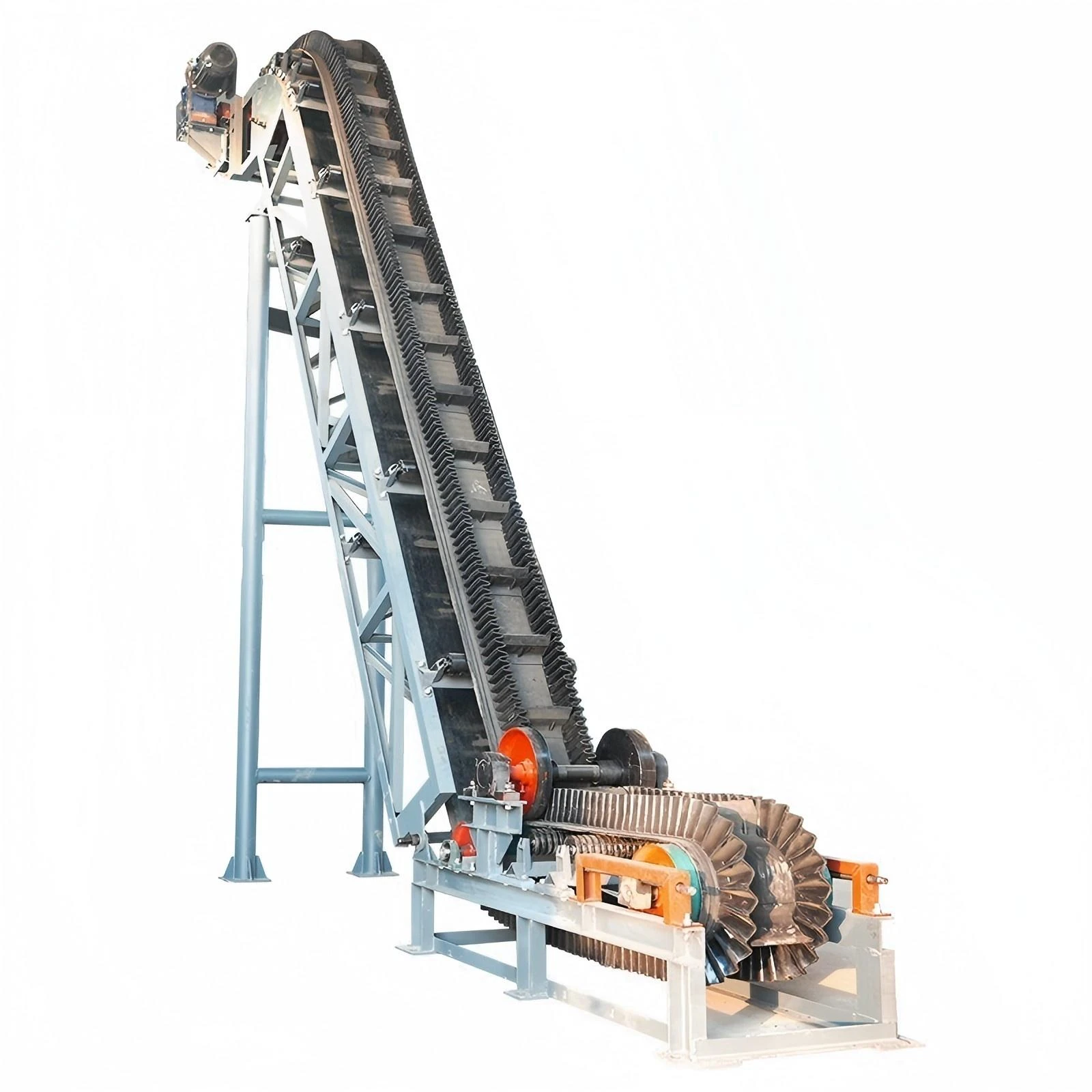
(belt conveyor for sale)
Why Modern Belt Conveyor for Sale Solutions Transform Material Handling
Operational efficiency becomes measurable when upgrading to specialized belt conveyor systems. Current industry analyses indicate facilities can achieve 40% higher throughput capacity and reduce labor costs by $11.30 per handled ton through automation. Particularly in bulk handling, conveyor technology eliminates manual transfer bottlenecks - an advantage critical in fertilizer production lines where particulate consistency directly impacts quality control. Operations switching from drag chain systems report 22% lower power consumption with belt-driven alternatives due to decreased friction resistance. Cleated belt conveyor installations demonstrate even greater ROI in inclined applications, securing materials at 35-degree inclines while maintaining 98% load retention.
Durability metrics further validate investment decisions. Episys monitoring indicates modern polymer-reinforced belts withstand over 65,000 operational hours before requiring replacement - a 300% lifespan improvement compared to early-generation rubber belts. When considering fertilizer belt conveyor for sale
options, this endurance becomes crucial given corrosive ammonium nitrate exposure. Production managers consistently report sub-18 month payback periods on conveyor investments, largely attributed to these engineered material breakthroughs. Continuous flow technology essentially transforms capital expenditure into sustained margin protection.
Engineering Advancements Driving Reliability
Recent design innovations address historical pain points in conveyor applications. Precision-tensioned belt tracking systems now maintain alignment within ±5mm variance, reducing edge wear incidents by 87% according to BulkPro testing data. Impact-resistant ceramic lagging on drive pulleys doubles component longevity under abrasive material conditions, while integrated belt misalignment sensors automatically trigger shutdowns before damage escalation. These engineering solutions directly correlate with measurable uptime improvements: facilities report less than 1.2% unscheduled downtime with contemporary designs.
Thermal-imaging sensors installed at critical bearing points detect temperature anomalies indicating lubrication failure 30-45 minutes before traditional vibration-based systems. This advancement alone prevents approximately 73% of catastrophic bearing failures in continuous operation scenarios. For operators evaluating cleated belt conveyor for sale options, enhanced cleat geometry with vulcanized reinforcement demonstrates 90% greater tear resistance during heavy-load startups. These quantifiable engineering advances shift conveyor systems from maintenance liabilities to production assets.
Material-Specific Configuration Considerations
Bulk material properties dictate precise conveyor specification requirements. When handling fertilizers, chemical compatibility becomes paramount. UHMW polyethylene liners demonstrate superior resistance to ammonium sulfate corrosion, with wear rates below 0.15mm/year versus stainless steel's 0.38mm/year degradation according to ASME B31.3 test protocols. Belt selection equally impacts operational safety: anti-static compounds prevent combustible dust ignition, crucial when handling powdered NPK blends where MIE (Minimum Ignition Energy) thresholds fall below 10mJ.
Angle of repose determines cleat spacing - materials like granular urea at 25° flow angles require 50% closer cleats than pelletized limestone (19°) to prevent backslide. Load calculations must incorporate impact forces: uncontrolled material drops exceeding 0.75m generate up to 6.7kN dynamic forces, necessitating reinforced impact beds. Proper specification eliminates common failure points before commissioning begins.
Manufacturer Capability Benchmarking
Manufacturer | Max Load Capacity (kg/m) | Fertilizer-Specific Design | Cleated System Depth (mm) | Maintenance Interval (hrs) |
---|---|---|---|---|
BulkTech Systems | 850 | Stainless steel construction | 40-120 | 2,500 |
ConveyPro Solutions | 1,200 | Corrosion-resistant polymer | 30-100 | 3,000 |
AgriFlow Dynamics | 650 | Specialized moisture seals | 25-85 | 3,500 |
Precision Movers | 1,500 | Integrated dust suppression | 50-150 | 2,000 |
The quantitative differences significantly impact long-term operational costs. ConveyPro's polymer construction demonstrates 23% lower annual ownership costs despite higher initial investment when handling acidic fertilizers. Precision Movers' heavy-duty design supports high-capacity operations but requires more frequent maintenance. AgriFlow's specialized sealing technology reduces fertilizer clumping by 18% in humid climates, demonstrating how targeted engineering solves environmental challenges.
Industry-Specific Adaptation Strategies
Modular engineering enables precise application solutions without requiring fully custom manufacturing. Three common adaptation scenarios showcase this flexibility. In granulation facilities, magnetic head pulleys integrate directly with conveyor frameworks, removing tramp metal contaminants at rates exceeding 98% efficiency. For high-volume distribution centers, variable-frequency drives modulate belt velocity between 0.8-4.2 m/s, synchronizing with automated sortation systems while maintaining constant torque. Cold-weather fertilizer operations implement heated troughing idlers that prevent material freezing at temperatures down to -40°C.
Cleated system enhancements address particularly challenging applications. Cleat geometry evolves for material-specific needs: steep-angle phosphate conveyance utilizes high-backed chevron designs at 75° angles versus standard 45° profiles. Belt width optimization demonstrates measurable output improvements: increasing fertilizer belt width from 900mm to 1200mm elevates throughput by 79% without requiring additional linear floor space. Operators leverage such data-driven modifications to overcome specific process limitations.
Documented Operational Improvements
Quantifiable results from current installations validate technical approaches. WestVista Fertilizers increased bagging line output by 33 tons/hour after implementing belt conveyors with dynamic weighing integration. Post-installation monitoring verified exact loading variances under 0.75% - a critical precision improvement for automated blending operations. The cleated incline system eliminated forklift transfers between elevations, reducing particulate emissions below 1.0 mg/m³ compliance thresholds.
MineralCorp's zinc pellet facility provides a contrasting application study. Their heavy-duty belt conveyor solution handles material impact forces exceeding 18 kJ, combining energy-absorbing impact beds with 10mm thick belts rated for 125 kN/m tensile strength. The conveyor replaced vibratory feeders that previously required quarterly screen replacements at $12,000 per maintenance event. Such targeted implementations demonstrate how material-specific conveyor designs resolve unique industrial challenges.
Securing Your Ideal Belt Conveyor for Sale
Procurement decisions require matching operational parameters with appropriate technologies. Critical specification factors include hourly throughput volume (range: 15-3000 TPH), temperature extremes (including seasonal variations), vertical lift requirements, and material abrasiveness classification. Fertilizer operations prioritizing longevity should request DIN 22102-certified belts with minimum 5-layer EP400 polyester reinforcement. Operations handling varying materials benefit from adjustable cleated belt conveyor configurations that adapt to changing product lines.
Pre-purchase inspections prevent compatibility issues: verifying frame dimension tolerances below ±1.5mm, motor mounting plate parallelism within 0.2° variance, and drum concentricity under 0.05mm runout. Reputable manufacturers provide certified test reports covering all dynamic load scenarios. Optimal procurement occurs when technical specifications align with verifiable performance data and lifecycle cost projections.
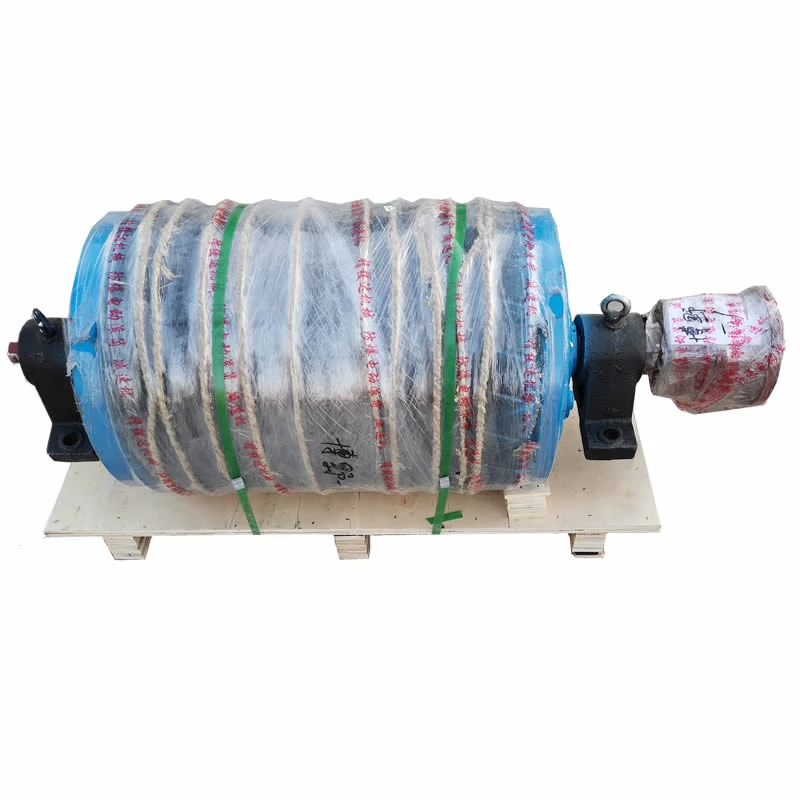
(belt conveyor for sale)
FAQS on belt conveyor for sale
Q: What types of belt conveyors are available for sale?
A: Our belt conveyor for sale range includes standard, fertilizer-specific, and cleated models. Each type caters to different industrial needs like bulk material handling or inclined transport. Options are customizable for efficiency and durability.
Q: Why choose a fertilizer belt conveyor for sale?
A: A fertilizer belt conveyor for sale is designed to handle bulk granules without spillage. Its corrosion-resistant materials ensure long-term reliability in agriculture settings. This enhances productivity for fertilizer processing and reduces waste.
Q: What makes a cleated belt conveyor for sale ideal for slopes?
A: The cleated belt conveyor for sale features raised sections that grip materials on inclines. This prevents slippage and boosts stability for tasks like grain loading. It’s cost-effective and easy to integrate into existing systems.
Q: How long does installation take for a belt conveyor purchased for sale?
A: Installation typically takes 1-3 days, depending on conveyor type and site complexity. Our team provides setup guides and remote support for quick assembly. For smooth operation, we recommend professional site preparation.
Q: Can I get a customized quote for a belt conveyor for sale?
A: Yes, we offer free quotes based on your specifications like length or capacity. Simply provide details through our online form or contact sales. This ensures a tailored solution without hidden costs.