- Fundamentals of static control in conveyor systems
- Technical specifications and material innovations
- Performance metrics and safety compliance standards
- Comparative analysis of leading manufacturers
- Customization approaches for industry-specific solutions
- Implementation case studies across sectors
- Future developments in static-dissipative technology
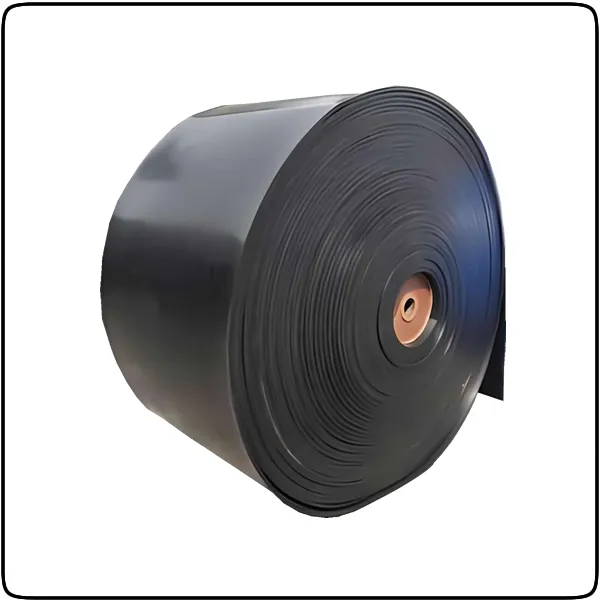
(anti static conveyor belt)
The Essential Role of Anti Static Conveyor Belts in Modern Industry
Electrostatic discharge (ESD) poses severe risks in material handling operations, with voltages regularly exceeding 30kV on standard conveyor systems. Anti static conveyor belts specifically engineered to dissipate charges below 35nC/square meter prevent these hazardous accumulations. Industries from semiconductor manufacturing to pharmaceutical packaging increasingly implement these solutions, as uncontrolled ESD events can damage microelectronics valued up to $5 billion annually according to EOS/ESD Association reports. These specialized belts maintain surface resistivity between 10^6 and 10^9 ohms/square - the critical range for safe static dissipation without attracting dust. The growing automation across logistics sectors (projected to reach $102 billion by 2028) further amplifies demand for reliable static control during high-speed transportation.
Technical Specifications and Material Innovations
Modern anti-static belts utilize carbon-infused thermoplastic polyurethane (TPU) compounds that achieve consistent 10^8 ohm resistivity throughout operational lifetimes. Unlike surface-coated alternatives that degrade after 6-9 months, through-material compounding maintains ESD protection for over 3 years of continuous service. Leading manufacturers like Habasit now incorporate conductive polyester yarns in warp direction weaving, creating static dissipation paths while maintaining <0.5% elongation under load. Thermoplastic elastomer formulations withstand temperatures from -40°F to 212°F without compromising ESD properties. Recent breakthroughs include graphene-enhanced compounds that reduce surface resistance to 10^6 ohms while increasing tensile strength to 45 MPa – 25% stronger than conventional ESD belts. These technical enhancements translate to 30% longer service intervals and reduced energy consumption.
Performance Metrics and Compliance Standards
Rigorous testing protocols govern anti-static conveyor systems, with IEC 61340-5-1 and ANSI/ESD S20.20 representing baseline certifications. High-performance belts must achieve charge decay rates below 0.5 seconds from 5kV to 100V while maintaining volume resistivity between 10^5 and 10^9 ohm-cm. Top-tier products exhibit consistent results after accelerated aging simulations equivalent to 15,000 operational hours. Operational metrics include >98% static dissipation efficiency at belt speeds up to 4.5m/sec. ATEX certification remains essential for combustible environments where static sparks could trigger explosions – compliant belts must limit surface voltage below 100V in methane-rich atmospheres. Third-party validation through organizations like TÜV SÜD provides crucial performance verification, with premium belts maintaining safety parameters across millions of duty cycles.
Manufacturer | Surface Resistivity (ohms/sq) | Charge Decay (sec) | Warranty (months) | Max Operating Temp (°F) |
---|---|---|---|---|
Intralox | 10^7 - 10^9 | 0.18 | 24 | 200 |
Habasit | 10^6 - 10^8 | 0.32 | 18 | 185 |
Sparks Belting | 10^8 - 10^9 | 0.25 | 12 | 175 |
Ammeraal Beltech | 10^7 - 10^10 | 0.21 | 18 | 190 |
Industry-Specific Customization Solutions
Effective static management requires tailoring solutions to operational environments. Food processing applications demand FDA/USDA-compliant materials with continuous-weld edges eliminating bacteria traps. For electronics assembly, manufacturers like Multi-Conveyor offer 1-meter wide belts with edge-to-edge resistivity variance under 3%. Pharmaceutical installations utilize static-dissipative silicone coatings achieving <0.1 micron surface roughness for delicate blister pack transfers. Mining operations utilize heavy-duty PVC formulations with 8mm cleats and carbon fiber plys for vertical inclines. The most advanced solutions incorporate modular thermoplastic segments (4x standard replacement efficiency) with customized track patterns. German manufacturer Forbo's proprietary ANTISTAT® technology allows zone-specific resistivity tuning, varying conductivity along belt length to address different static challenges within single production lines.
Operational Case Studies Across Sectors
Global automaker BMW integrated static-dissipative belts across their Leipzig assembly lines, reducing electrostatic paint defects by 87% while improving part transfer precision to 0.05mm tolerance. A leading contract electronics manufacturer resolved previously chronic CMOS sensor rejection rates (historically 4.2%) through comprehensive static control implementation including specialized conveyors. Post-implementation defects decreased to 0.3%, translating to $3.7 million annual savings. In powder handling, a Canadian chemical processor eliminated combustible dust incidents after replacing conventional belts with Sparks Belting's anti static conveyor belt
system featuring ATEX-certified polyurethane construction. The installation documented consistent surface voltage suppression below 50V in explosive atmospheres. Most recently, semiconductor facilities producing 3nm chips adopted vacuum-compatible stainless steel mesh belts with embedded carbon pathways maintaining <1KV surface voltage in ultra-low humidity cleanrooms.
Advancing Anti Static Conveyor Belt Technologies
Emerging IoT integrations now enable real-time static monitoring through embedded sensors transmitting conductivity data to predictive maintenance systems. Material innovations focus on self-regulating conductive polymers that adapt resistivity to environmental humidity fluctuations. European researchers recently demonstrated carbon nanotube-infused belts achieving 10^5 ohm resistivity with 40% less conductive filler material. Industry leaders project mainstream adoption of anti static conveyor belt systems featuring photo-induced conductivity within 5 years – using UV exposure to modulate resistance dynamically without mechanical additives. These developments address growing demands from renewable energy component manufacturing where mega-scale static discharges pose unique handling challenges. Current R&D pipelines target cost reductions through recycled conductive composites, potentially decreasing premium pricing by 20-25% while maintaining required ESD protection standards for high-value manufacturing operations.
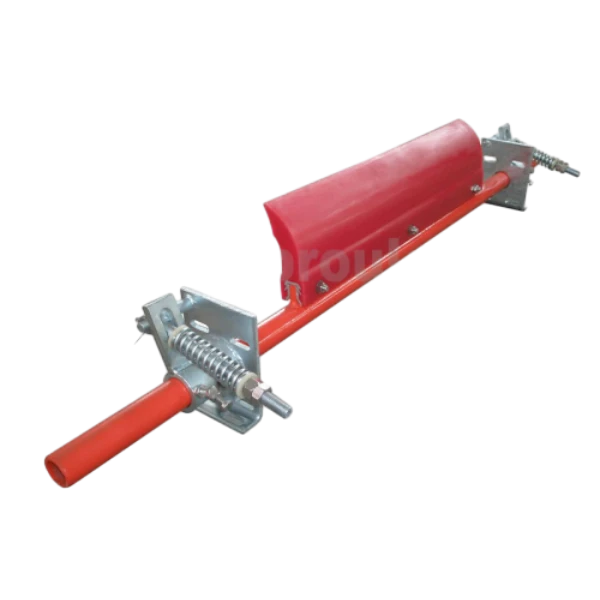
(anti static conveyor belt)
FAQS on anti static conveyor belt
以下是围绕核心关键词[anti static conveyor belt]及其相关词创建的5组英文FAQ问答,符合要求并以HTML富文本格式呈现:Q: What is an anti static conveyor belt?
A: An anti static conveyor belt is designed to dissipate static electricity during material transportation. It prevents sparks or electrostatic discharge that could damage sensitive products or ignite flammable materials. Special conductive materials or carbon fibers are integrated into its structure.
Q: How does an anti static conveyor belt work?
A: It uses conductive elements woven into the belt fabric to create a controlled path for static electricity. This directs charges safely to ground points via pulley systems. Regular testing with surface resistance meters ensures continuous effectiveness.
Q: Where are anti static conveyor belts essential?
A: Critical in electronics manufacturing to prevent component damage from electrostatic discharge. Also vital in chemical/pharmaceutical plants where sparks could ignite flammable substances. Printing and packaging facilities use them to avoid sheet sticking issues.
Q: How do I maintain anti static properties in conveyor belts?
A: Perform monthly surface resistance tests using specialized meters. Keep belts clean with approved anti static cleaners to prevent residue buildup. Replace worn sections immediately as cracks compromise conductivity.
Q: What's the difference between anti static and standard conveyor belts?
A: Anti static belts feature embedded conductive materials (carbon/steel fibers) unlike standard belts. They maintain surface resistance below 10¹¹ ohms/sqr for safe discharge. Standard belts exceed this threshold, posing higher static risks.